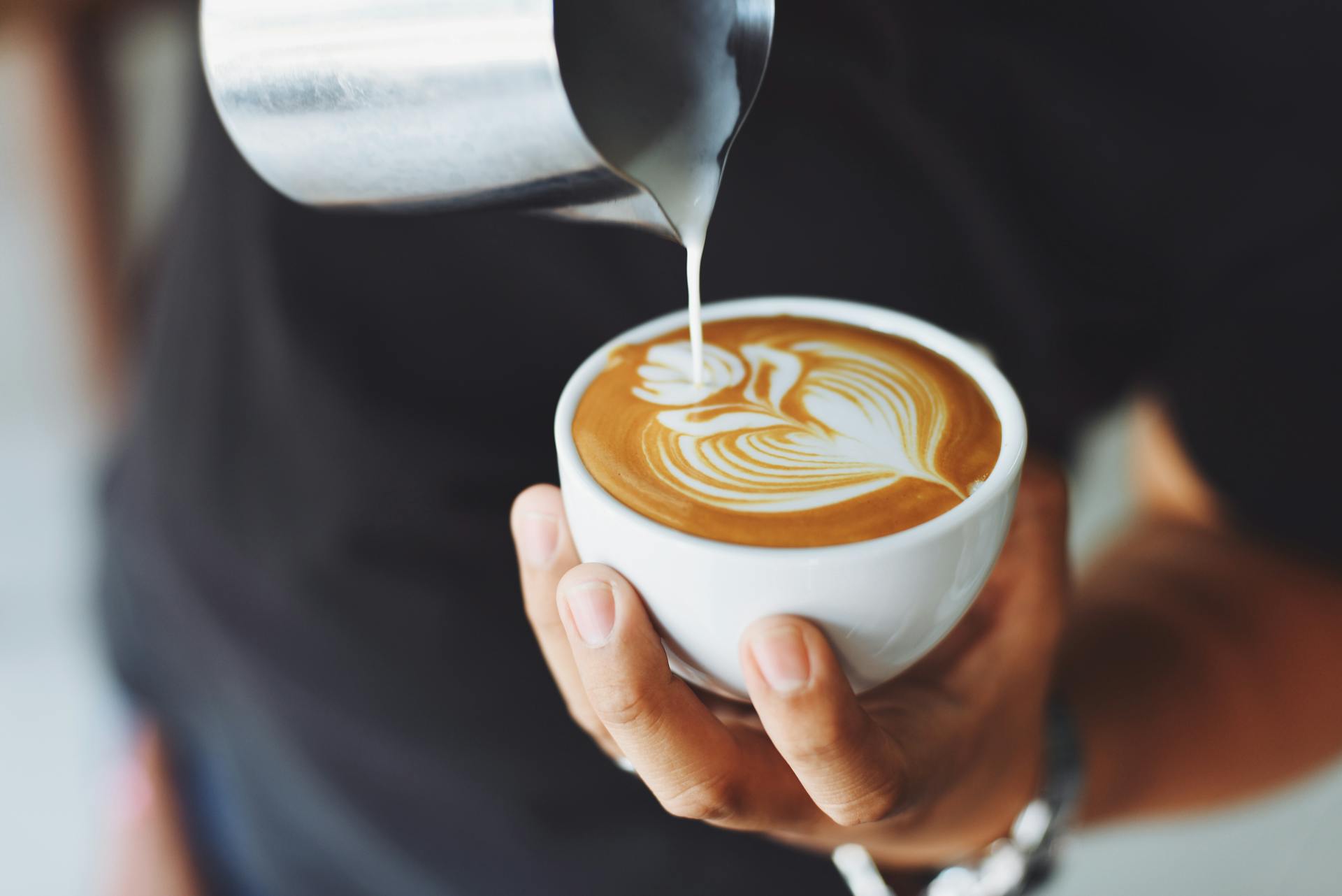
Foam architectural models are a staple in the design world, offering a tangible representation of a building's design. They can be created using various techniques, including 3D printing and manual carving.
These models can be used for presentations, client meetings, and even as a tool for designers to visualize and refine their ideas. The level of detail can range from simple to highly intricate, depending on the design's complexity.
Foam models are often preferred for their affordability and durability compared to other materials like wood or foam board. They can withstand handling and display without significant damage.
A unique perspective: Pavilion Roof Design
Benefits of Board Modeling
Building with foam core is the preferred method for scale model making because it's easy to use and provides the right rigidity.
Regular white foam board is a good starting point, but it's essential to get it from a reliable source to ensure proper quality.
Gatorfoam is a pricier option, but it offers cleaner cuts, crisper edges, and a more resistant surface to dents.
Self-adhesive foam board is also a great investment, as it can serve as a sturdy base for your model.
Having the right materials can make all the difference in the quality of your foam architectural models.
You might like: Architectural Drafting Board
Modeling Tools and Techniques
When working with foam architectural models, you'll want to have the right tools to create a precise and detailed design. A good starting point is to invest in specialized cutting tools designed for foam core, which will help you achieve clean cuts and beveled edges.
To cut small circles, a drill can be a lifesaver. Double-sided tape is also a valuable asset, allowing you to temporarily hold pieces in place until you can affix them permanently.
A straight edge is essential for making precise cuts, and a T-square can be a good alternative to specialized rulers designed for foam modeling. Pins can be used to provide added reinforcement for walls, but be sure they're not sticking out when you're finished.
You'll also want to have a variety of hand tools on hand, such as Dremel tools, die grinders, and electric knives, to refine your design and add finer details.
Here are some essential tools to get you started:
- Cutters: Specialized tools for foam core
- Drills: For cutting small circles
- Tapes: Double-sided tape and framer's tape
- Straight Edge: Specialized rulers or a T-square
- Pins: For added reinforcement
- Hand tools: Dremel tools, die grinders, and electric knives
When choosing the right foam for your model, consider using expanded polystyrene foam (EPS), which offers a good balance between affordability, ease of use, and durability. This type of foam can be purchased in sheets or blocks, and can be glued together to create thicker pieces.
It's also worth noting that different densities of foam are available, ranging from 1 lb to 3 lb, with 2 lb density being a good all-around choice.
Technology and Materials
Polystyrene foam is a popular choice for foam architectural models due to its tough, lightweight, and economical nature. It's often used for large-scale models that make a statement and showcase a brand in new and creative ways.
A 2 lb density foam is a good compromise between affordability, ease of use, and durability. It's a balance between the density of foam that's important, as lower density foam is easier to cut and manipulate while higher density foam allows for finer details.
Foam models require sculpting, carving, special finishes, coatings, and various other skill sets to build. Examples of these skills include using a grid system to mark areas in need of sculpting and using a heated wire to carve the foam.
The right balance of density is crucial, as lower density foam is prone to damages such as cracking or shedding. Treating foam models with care is essential to ensure they last.
Combining traditional foam sculpting and cutting techniques with new 3D printing capabilities allows model makers to build impressive and detailed models. This fusion of technologies enables the creation of complex designs and precise details.
Frequently Asked Questions
What is the best foam for model building?
For model building, XPS Modelling Foam is a top choice due to its lightweight and strong properties. It's easy to shape and cut, making it perfect for creating 3D models and structures.
Sources
- https://foamboards.com/blogs/the-board-blog/guide-to-making-foam-board-architectural-models
- https://www.blueprintmodels.com/materials-used-in-architectural-scale-models-rigid-foam-polystyrene/
- https://www.blueprintmodels.com/choosing-the-right-materials-for-architectural-models/
- https://www.whiteclouds.com/3d-technology/foam-models/
- https://model-makers.co.uk/materials-for-architectural-models/
Featured Images: pexels.com