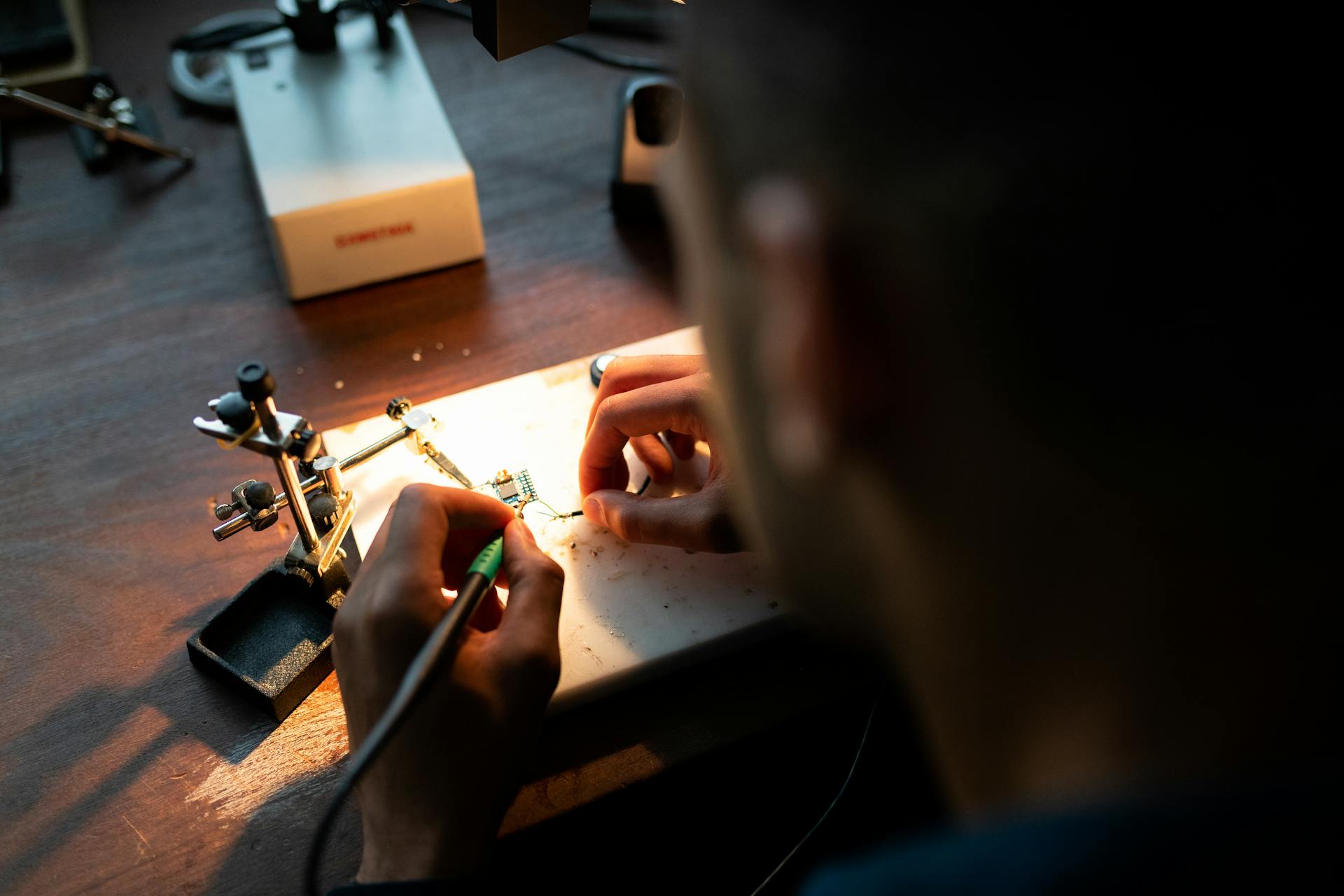
Soldering copper pipes with water in them requires a bit of finesse, but with the right techniques, you can get the job done safely and efficiently.
First, make sure the pipe is completely drained of water before attempting to solder it. This is crucial to avoid any accidents or damage to the pipe.
To drain the pipe, turn off the main water supply and open the lowest faucet or valve to allow the water to drain out. This will help prevent any water from flowing back into the pipe while you work.
Once the pipe is drained, use a flux to clean and prepare the surface for soldering.
Materials and Preparation
To solder copper pipes with water in them, you'll need the right materials. Copper tubing of the proper diameter is essential, and it's available in various sizes, with the outside diameter being 1/8" larger than its stated size.
When selecting the tubing, make sure it's of the proper wall thickness for your project. Most nominally-sized copper tubing is available in four weights, or wall thicknesses, which are color-coded. For residential projects, Type L or M is usually sufficient.
You'll also need the proper connectors and joints for your system. This will depend on your project, but you'll likely need some combination of elbows, tees, and couplings.
For soldering, you'll need lead-free solid core solder, typically 95/5 (95% tin and 5% antimony), or an alloy of tin and a small amount of copper and/or silver.
To prepare your copper pipes for soldering, you'll need a copper pipe brush to clean the outside of the pipe and the inside of the fitting. You should also inspect the pipe and fitting for burrs and clean them further if necessary.
Here's a list of materials you'll need for this project:
- Copper tubing
- Solder
- Flux with flux brush
- Propane or acetylene torch
- Fire extinguisher
- Sandpaper
- Copper tubing reamer
- Tubing cutters
Remember to always use a heat source of sufficient output capacity to heat the assembled fittings and tubing to a temperature above that required to melt the filler solder, typically 400 to 500 °F (204 to 260 °C).
Take a look at this: How to Install Heat Cable on Water Pipes
Cutting and Cleaning
To get started with soldering copper pipes, you'll first need to cut and clean the pipes and fittings. Measure and cut the copper pipe to the desired length using a tube cutter, making sure the cut is square.
It's essential to deburr and clean the pipe surface to ensure a smooth soldering process. Use a sand cloth, open mesh cloth, nylon grit pad, or tube cleaning brush to clean the outside and inside of the pipe.
A clean joint is crucial for a watertight seal. To clean the joint, thoroughly burnish the fitting inside and out with a wire brush or emery cloth, then wipe with a clean cloth.
Remember to be careful not to touch the polished surfaces, as dirt or grease can interfere with the capillary action of the solder. This is especially important, as the oil from your fingertips can also cause issues.
By following these steps, you'll be able to create a clean and smooth surface for soldering. A clean pipe and fitting will help the solder flow evenly, forming a watertight joint.
Consider reading: Flushing Water Pipes in House
Soldering
Soldering copper pipes with water in them can be a bit tricky, but with the right technique, you'll be able to get the job done efficiently.
Most solder melts at 324 degrees Fahrenheit, which is crucial to know when working with propane torches. A cheap propane torch works best when the cone in the center is 1.5 inches in height, allowing the pipe to heat up in about 30 seconds.
To obtain the right temperature, keep in mind that most torches produce more flame when tilted downward. Be careful to hold the torch in a consistent way to avoid accidents.
Light the propane torch and turn the flame to medium, pointing it directly at the joint. The joint will heat up after about 20-60 seconds.
If you're soldering a valve, it's better to open the valve to reduce the risk of damage to the valve.
Touch the solder to the crease between the fitting and the pipe, and when the joint is hot enough, the solder will melt and capillary action will pull the solder into the joint.
As the solder starts to melt, move it all the way around the joint. When solder pools outside the joint, the joint is stable.
Turn off the heat and allow the pipe to cool. Clean away excess flux with a damp rag, as it can corrode the pipe and later cause pinhole leaks to form.
Here are some additional tips to keep in mind:
- Clean the surface of the tubing and the inside of the fitting thoroughly before applying flux.
- Continue to push the solder into the joint as the pipe cools to ensure it's completely full of solder and there are no leaks.
Sources
- https://www.finehomebuilding.com/forum/need-to-solder-wet-copper-pipes
- https://www.oatey.com/how-solder-copper-pipes
- https://www.1tomplumber.com/sweating-pipes-step-by-step/
- https://www.wikihow.com/Solder-Copper-Tubing
- https://www.oneprojectcloser.com/how-to-sweat-solder-copper-water-pipes-for-a-watertight-seal/
Featured Images: pexels.com