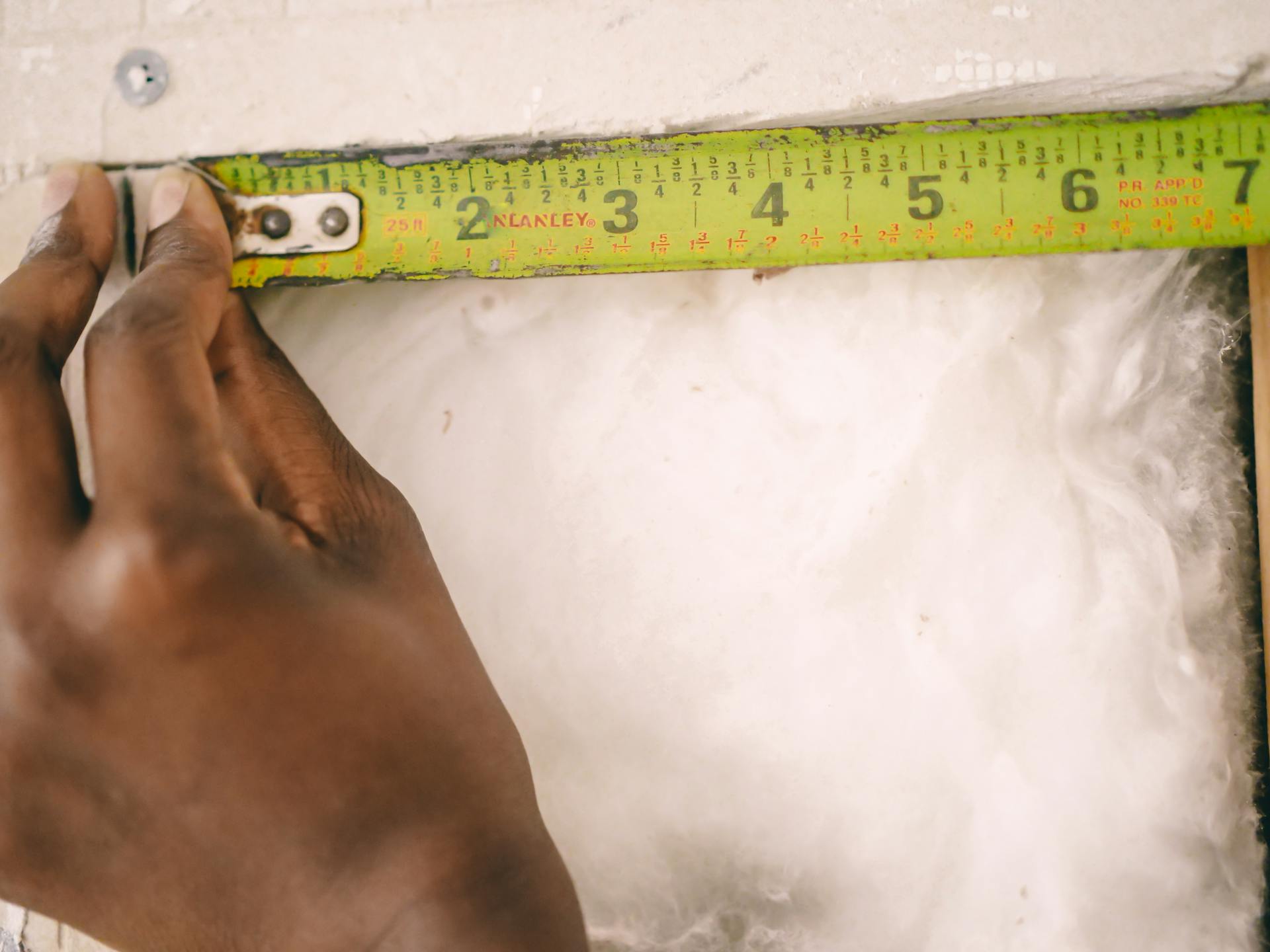
Proper insulation for your roof with attic is crucial to prevent heat loss and reduce energy bills.
Loft insulation is a must-have for homes with attics, as it can save up to 30% of energy costs.
The recommended loft insulation depth is between 270 and 300mm, which is equivalent to 10-12 inches of insulation material.
Insulation Materials
Fiberglass batt is considered the best insulation for attics, being the cheapest and easiest to install. It's also incredibly energy efficient, helping to slow the spread of hot and cold air.
Fiberglass batt insulation comes in mold and mildew-resistant forms, making it a great choice for homes prone to moisture. It's also made of recycled sand and glass, making it a more environmentally friendly option.
If you're looking for alternative insulation materials, consider cellulose, mineral wool, or cotton. Cotton has an R-value of 3.0 to 4.0 per inch, making it a good choice for those who want to reduce their environmental impact.
Here are some key characteristics of common insulation materials:
Mineral wool insulation is a good choice for homes with noise pollution issues, as it blocks sound more effectively than other insulators.
Fiberglass Batt Material
Fiberglass batt is the cheapest insulation material for attics. It's also the easiest to install.
Fiberglass batt is incredibly energy efficient, slowing the spread of hot and cold air to keep your house cool in the summer and warm in the winter. This is a big plus for homeowners who want to save on energy bills.
Fiberglass batt insulation prevents unwanted pollutants from entering your home, improving air quality. It comes in mold and mildew-resistant forms, so you don't have to worry about mold growing in your attic.
Fiberglass batt is made from recycled sand and glass, making it an eco-friendly option. Its lightweight and flame-resistant composition is another bonus.
Fiberglass rolls are a great option for insulating wide-open areas in your attic. They contain the same insulation material as fiberglass batts but come in longer segments that you can roll out.
Using fiberglass rolls decreases the likelihood of gaps in your insulation, making them a good choice for large areas.
If this caught your attention, see: Roof and Attic Insulation
Mineral Wool
Mineral wool is a fiber insulation made from natural materials, offering an alternative to fiberglass insulation. It has an R-value of 3.1 to 4.0 per inch when blown in, and 3.1 to 3.4 per inch when installed in batts.
Mineral wool is naturally resistant to moisture, making it an excellent choice for homes prone to mold and mildew growth. This is especially important for homes with poor ventilation or those located in humid climates.
One of the standout benefits of mineral wool is its ability to block sound. It's more effective than any other insulator, making it a great choice for homes with noisy neighbors or those located near busy roadways.
Mineral wool insulation is typically composed of 75% recycled materials, making it an eco-friendly option for homeowners. However, it's essential to note that protective gear must be worn during installation to avoid lung disease caused by inhaling the fibers.
Curious to learn more? Check out: Types of Roof Materials
Mineral wool can compress and leave gaps as it ages, which may compromise its insulating performance. Additionally, it can be challenging to dry if it becomes wet, so it's crucial to ensure proper installation and maintenance.
Here are some key pros and cons of mineral wool insulation:
- Naturally fire resistant
- More effective than fiberglass insulation
- Typically composed of 75% recycled materials
- Protective gear must be worn during installation
- Can compress and leave gaps as it ages
- Hard to dry if it becomes wet
- More expensive than other materials
Radiant Barrier
Radiant barriers are a great option for warm climates experiencing hot weather, providing a cooling effect that's fairly easy to install.
They work best on sloped roofs that are perpendicular to the direction of the sun.
In warmer climates, radiant barriers can be a cost-effective solution, with prices ranging from $50 cents to $1.00 per sq. ft. for DIY installation.
However, if you hire a professional, be prepared to pay closer to $2.00 per sq. ft.
Installation and Preparation
Before installing insulation in your attic, it's essential to prepare the space. Seal air leaks and bypasses as described previously, and verify attic air-tightness. Repair roof leaks and remove other moisture sources before insulating the attic.
To ensure safe and effective insulation, vent all kitchen and bath fans outdoors through appropriate roof fittings, side wall fittings, or soffit fittings. Install an attic access hatch if none is present, preferably at a large gable vent on the home's exterior. An interior attic hatch should be at least 22 inches square if possible.
Here are some key steps to take before installing insulation:
- Seal air leaks and bypasses
- Verify attic air-tightness
- Repair roof leaks and remove moisture sources
- Vent kitchen and bath fans outdoors
- Install an attic access hatch
Preparing for
Before you start insulating your attic, make sure to seal any air leaks and bypasses as described in the "Air-Sealing Attics and Roofs" section on page 111. This will ensure a tight seal and prevent heat from escaping.
It's also essential to repair any roof leaks, remove moisture sources, and fix other attic-related moisture problems before insulating. This will prevent any further damage and ensure a successful insulation job.
Venting kitchen and bath fans outdoors is crucial to prevent moisture buildup in the attic. This can be done by installing roof fittings, side wall fittings, or soffit fittings.
Installing an attic access hatch is also a must, especially if you don't have one already. This will provide safe and easy access to the attic for future maintenance and repairs.
If you do need to install an interior attic hatch, make sure it's at least 22 inches square and insulate it to the maximum practical R-value. The roof's height above the hatch may limit the amount of rigid board foam you can attach to the back of the hatch door.
Don't forget to document the insulation type, installed thickness, coverage area, and insulation R-value to post in the attic after installation. This will be helpful for future reference and maintenance.
Building an insulation dam around the attic access hatch is also a good idea. This can be done using rigid materials like plywood or oriented-strand board, and should be built two inches above the height of the insulation.
If head space is limited at the hatch, consider using fiberglass batts to dam loose fill insulation.
For another approach, see: Roof Insulation R Value
Box Out Light Fixtures
Cover any light fixtures that are placed near your installation area. If your insulation touches a light it can become a fire hazard.
Unless your light fixtures are rated safe for contact with insulation, make sure to cover them in plywood, metal, or hardware cloth. This is especially important for non-IC-rated fixtures that must not touch insulation.
You can also consider removing the recessed light fixture and replacing it with a surface-mount fixture. This is a good option if you're planning to install new insulation in the attic.
Here are some options to consider when preparing recessed light fixtures for attic insulation:
Remember, spray foam insulation must not cover or surround recessed light fixtures or any other heat-producing devices.
Redirect Exhaust Fans
Redirecting exhaust fans is a crucial step in ensuring your home is properly ventilated. Many homes have vents directed into the attic, which can cause humid air to ruin your insulation.
This can lead to a range of problems, including mold growth, insulation damage, and even structural issues. In fact, building regulations prevent home builders from venting exhaust into an attic space for this very reason.
Correcting this issue is relatively simple and can be done by redirecting the exhaust fans to the exterior of your home. This will help to prevent humid air from accumulating in your attic and causing damage.
Related reading: Best Insulation for Mobile Home Roof
Finished Knee Wall
Finished knee wall attics require special attention when it comes to insulation. They often have five separate sections that need different air-sealing and insulating methods.
Inspect the structure to confirm it can support the weight of the insulation. This is crucial to avoid any structural issues.
Remove planking and insulation from the side-attic floor if necessary to expose air leaks. This will help you seal them properly.
Insulate access hatches to the approximate R-value of the assembly they're located in. This ensures consistent insulation throughout the attic.
Post an insulation certificate at the attic entrance. This certificate should include the type and number of bags installed, installed thickness, coverage area, and insulation R-value.
Blowing into a Cavity
Blowing into a cavity can be a bit tricky, but with the right technique, you can get the job done efficiently. Always use a fill tube when blowing closed roof cavities.
To access the cavity, you can insert the tube into the cavity to within a foot of the end of the cavity through the eaves, the roof ridge, the roof deck, or the ceiling. There are a few procedures to consider, such as drilling holes in the roof deck after removing shingles or ridge roofing, removing the soffit and blowing insulation from the eaves, or carefully removing a tongue-and-groove ceiling plank and blowing insulation into cavities through this slot.
Drilling holes in the roof deck requires removing shingles or ridge roofing, while removing the soffit is a better option for blowing insulation from the eaves. Carefully removing a tongue-and-groove ceiling plank can also be a viable option for blowing insulation into cavities.
For another approach, see: Roofing a Gambrel Roof Shed
For a more detailed approach, consider the following steps:
• Drill holes in the roof deck after removing shingles or ridge roofing.
• Remove the soffit and blow insulation from the eaves.
• Carefully remove a tongue-and-groove ceiling plank and blow insulation into cavities through this slot.
These procedures can help you access the cavity and blow insulation in the right way.
Closed Cavities
Closed cavities can be a challenge to insulate, but with the right preparation and installation, you can ensure a safe and energy-efficient space.
Many homes have cathedral ceilings or flat roofs that are partially filled with fibrous insulation, which can be a problem if not ventilated properly.
To prepare for roof-cavity insulation, you'll need to verify or provide a ventilated space of at least one inch between the roof insulation and the roof sheathing along with soffit and ridge ventilation.
If no roof ventilation, then install foam roof insulation in addition to filling the cavity insulation with fibrous insulation.
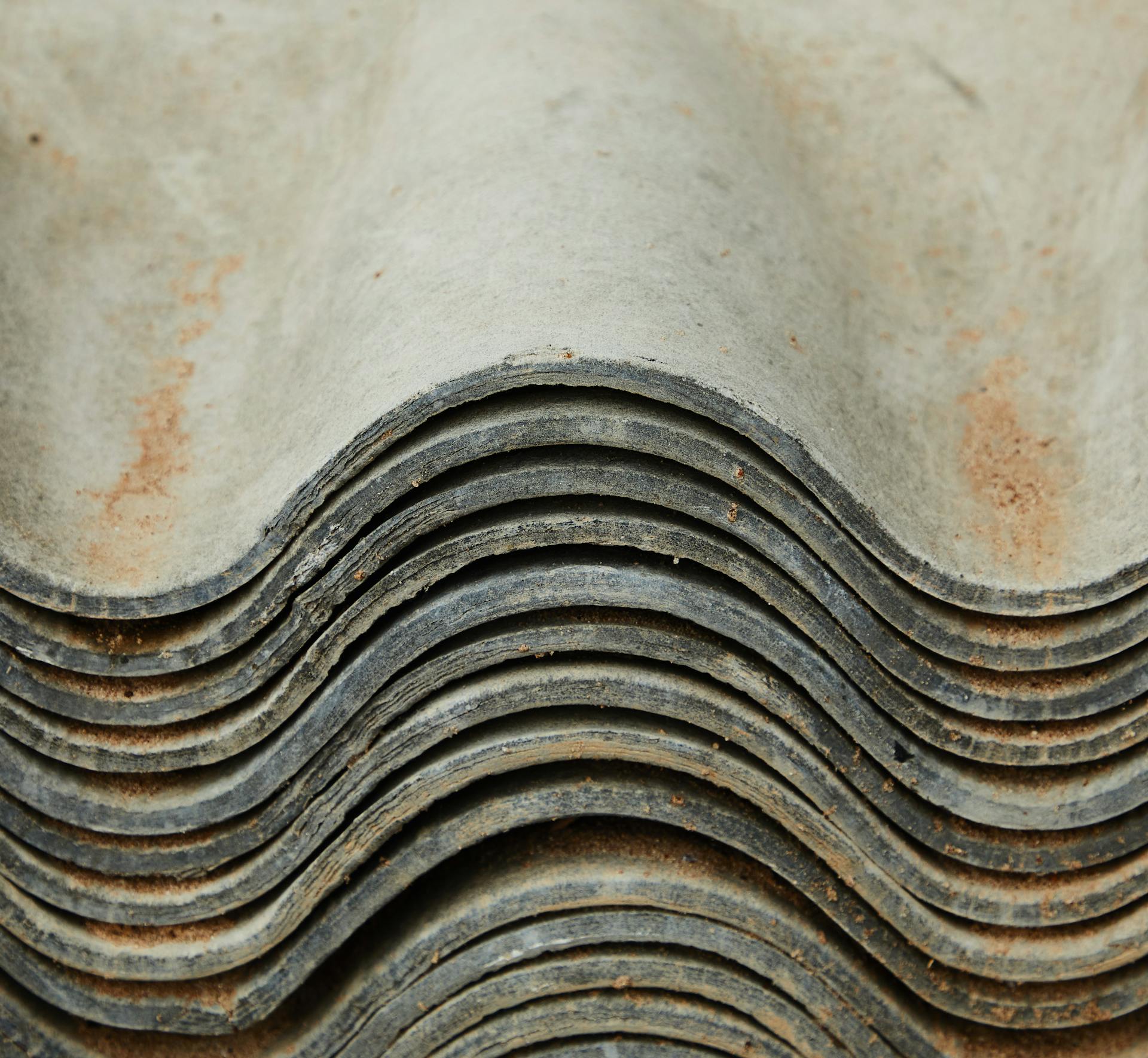
Dense-packing the cavities prevents most convection and moist-air infiltration, which are leading causes of moisture problems in roof cavities.
However, whether roof cavities can be safely dense-packed with fiberglass insulation and without ventilation is controversial and depends on climate.
The colder the climate, the higher the risk of ice damming or moisture damage to the structural sheathing if the roof deck is uninsulated.
To prepare for dense-packing the roof-cavity, consider the following steps:
- Verify that the ceiling has a Class I or II vapor retarder and air barrier on the interior.
- Remove recessed light fixtures and replace them with IC-AT fixtures or surface-mounted fixtures.
- Seal other ceiling air leaks, large and small, with great care.
- Install 1-to-8 inches of rigid high-density foam insulation on top of the roof deck if you replace the roof.
Here's a summary of the two approaches to insulate a roof cavity:
It's essential to consult a knowledgeable local engineer before deciding to dense-pack a roof cavity with fiberglass without tearing off the roof, insulating the roof deck, and re-roofing.
Electrical Junction Boxes
As you prepare your attic for insulation, don't forget about the electrical junction boxes. Install covers on all electrical junction boxes that lack covers. This is a crucial step to ensure safety and prevent any potential electrical hazards.
You'll also want to air seal electrical boxes that penetrate the ceiling, such as those for light fixtures and fans, before blowing fibrous insulation over the boxes. Use caulk or two-part foam for this purpose.
It's also a good idea to flag the electrical boxes so that an electrician can find them for future electrical work. This will save you time and hassle in the long run.
Installing Fiberglass Batts
Installing fiberglass batts in attics requires some planning and care. You should install new layers at right angles to underlying layers if the top of the existing batts are level with or above the ceiling joist or truss bottom chord.
Cutting batts carefully is essential to ensure a tight fit against the ceiling joists and other framing. This will help prevent gaps in the insulation.
If you must install faced batts, it's crucial to install them with the facing toward the heated space. This is to ensure the insulation is effective and safe.
Never install faced insulation over existing insulation, as this can compromise its performance and create safety hazards.
To minimize waste and ensure a snug fit, cut batts to size before installing them. This will also help you avoid having to cut them in place, which can be messy and time-consuming.
A key consideration when installing fiberglass batts is to ensure they are properly aligned and secured to the ceiling joists and other framing members. This will help maintain the integrity of the insulation and prevent it from shifting or settling over time.
Related reading: How to Cut Rafters for a Shed Roof
Installing Fiberglass Deck
Installing a fiberglass deck can be a bit of a challenge, but with the right preparation, you'll be enjoying your new outdoor space in no time.
First, make sure you have a solid foundation. According to the article, a concrete slab or a pressure-treated wood deck is the best base for a fiberglass deck.
Choose a fiberglass deck material that's suitable for your climate. In areas with high humidity, a marine-grade fiberglass is recommended. This type of fiberglass is designed to withstand moisture and salt exposure.
For your interest: Deck Lean to Roof
Measure your deck area carefully to determine how much material you'll need. A general rule of thumb is to add 10-15% to your total square footage to account for cuts and waste.
Cut the fiberglass sheets to size using a utility knife or a power saw. It's essential to make clean cuts to avoid damaging the material.
Secure the fiberglass sheets to the deck frame using screws or nails. Be sure to space them evenly, about 6-8 inches apart, to maintain a sturdy structure.
Apply a layer of sealant to the fiberglass deck to protect it from the elements. A silicone-based sealant is recommended for its water-resistant properties and ease of application.
Take a look at this: Shed Roof over Deck
Frequently Asked Questions
Should you insulate the underside of your roof?
Yes, insulating the underside of your roof is a recommended practice to prevent heat loss and gain, but it's even more effective when combined with attic floor insulation. This dual insulation approach can significantly enhance comfort in both winter and summer.
Is roof insulation the same as attic insulation?
No, roof insulation and attic insulation serve different purposes, with roof insulation keeping the attic cool and attic insulation keeping the rooms below warm and cool. Understanding the difference can help you choose the right insulation for your home's specific needs.
Sources
- https://www.ambientedge.com/kingman-heating-and-air-conditioning-repair-and-service-experts/what-is-the-best-insulation-for-the-attic/
- http://wxfieldguide.com/md/MarylandWxFg/AtticsRoofs/Insulating_Attics_and_Roofs.htm
- https://www.roofingcalc.com/roof-attic-insulation-options-and-costs/
- https://www.drenergysaver.com/insulation/attic-insulation/superattic-system.html
- https://goroofitright.com/the-dos-and-donts-of-spray-foam-insulation/
Featured Images: pexels.com