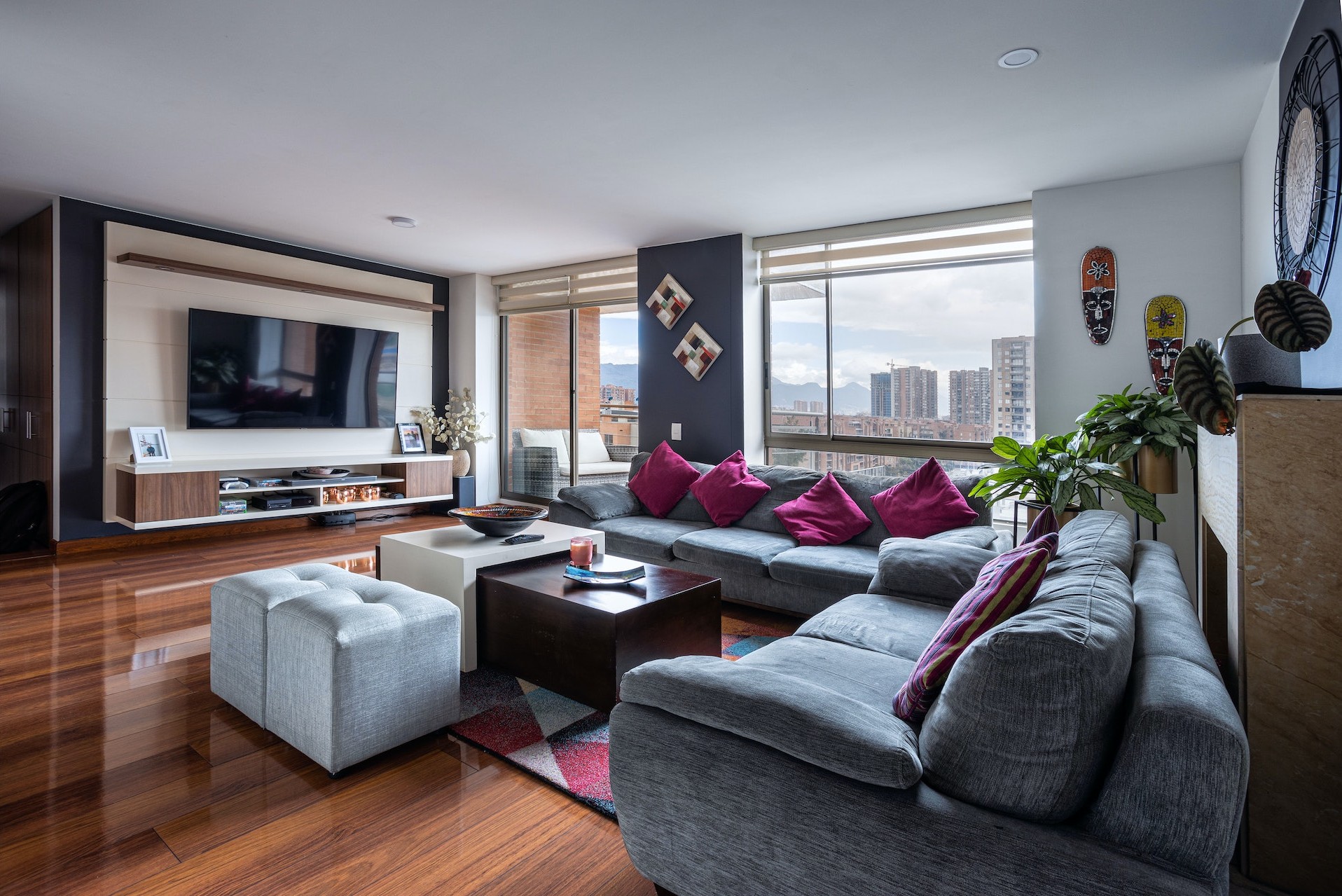
There are a few different schools of thought when it comes to quality management (QM) tools, but the most common tqm tools are those that fall into the "prevention" category. These are tools that help you to prevent defects from occurring in the first place, rather than trying to fix them after the fact. The most common tqm tools in this category are things like process mapping and process improvement plans.
However, there are a few other tqm tools that don't quite fit into this prevention category. These are tools that are more focused on helping you to identify defects after they've already occurred. The most common tqm tool in this category is a tool called a "control chart." Control charts help you to identify when a process is starting to produce more defects than usual, so that you can take corrective action before the situation gets out of hand.
So, which of the following is not a common tqm tool? The answer is that it depends on how you define "common." If you consider only those tools that fall into the prevention category, then the answer is control charts. However, if you consider all of the different types of tqm tools, then the answer is that all of the tools mentioned above are quite common.
What is not a common tqm tool?
There are a number of quality management tools that are not commonly used. These include:
1. Critical path analysis: This is a technique used to identify the activities that must be completed in order to complete a project on time. It is particularly useful for projects that have a lot of interdependent activities.
2. Value stream mapping: This is a technique used to map out the steps involved in a process. It is useful for understanding how value is added at each step and for identifying areas where waste can be reduced.
3. Process flowcharting: This is a technique used to map out the steps involved in a process. It is useful for understanding how value is added at each step and for identifying areas where waste can be reduced.
4. Failure mode and effects analysis: This is a technique used to identify potential problems that could occur during a process and the consequences of those problems. It is useful for identifying areas where process improvements can be made.
5. Statistical process control: This is a technique used to monitor and control a process using statistical methods. It is useful for ensuring that a process is stable and for identifying areas where process improvements can be made.
6. Design of experiments: This is a technique used to test different process variables to determine their effect on the output of a process. It is useful for understanding how process improvements can be made.
7. Total quality management: This is a technique used to manage the quality of a process from start to finish. It is useful for ensuring that a process is meeting quality standards and for identifying areas where process improvements can be made.
8. Benchmarking: This is a technique used to compare a process to other processes in order to identify areas where improvements can be made. It is useful for understanding how a process stacks up against others and for identifying areas where process improvements can be made.
9. Process capability analysis: This is a technique used to assess the ability of a process to meet specifications. It is useful for understanding how a process can be improved to meet quality standards.
10. Six Sigma: This is a technique used to manage process variation and to achieve extremely high levels of quality. It is useful for ensuring that a process is meeting quality standards and for identifying areas where process improvements can be made.
A different take: Where to Donate Used Tools?
What are the benefits of using a common tqm tool?
There are many benefits of using a common total quality management (TQM) tool. One is that it helps to ensure that everyone in an organization is using the same terminology and process when talking about quality. This can minimize confusion and help team members to communicate more effectively with one another. Additionally, a common TQM tool can help to standardize quality practices across an organization, which can make it easier to monitor progress and identify areas in need of improvement.
Another benefit of using a common TQM tool is that it can help to create a sense of ownership and buy-in from team members. When everyone is using the same tool, it can help people to feel more invested in the quality process and also gives them a common reference point to turn to when they have questions or need assistance. Additionally, using a common TQM tool can help to build team cohesion and morale, as people feel more united in their efforts to improve quality.
Finally, using a common TQM tool can help to save time and money in the long run. By having a standardized quality process in place, organizations can avoid the need for duplicate efforts or rework down the line. Additionally, using a common TQM tool can help to prevent errors and improve efficiency, both of which can save the organization money. In short, the benefits of using a common TQM tool are many and varied, and can provide a real boost to any organization’s quality management efforts.
What are the drawbacks of using a common tqm tool?
There are a number of potential drawbacks associated with using a common tool for TQM. One of the most significant potential drawbacks is that it can lead to a false sense of security. If all businesses in a particular industry or sector are using the same tool for TQM, it can give them a false sense of security in terms of their quality management processes. This false sense of security can ultimately lead to complacency and a failure to properly address quality issues. Additionally, if the common tool is not effective, it can lead to a waste of time and resources for all businesses using it. Another potential drawback of using a common TQM tool is that it can create a competitive disadvantage for businesses that do not use the tool. If all of your competitors are using a certain tool and you are not, it can put you at a disadvantage in terms of quality management. Additionally, using a common TQM tool can also lead to a loss of flexibility. If all businesses are using the same tool, they may all have to make changes to their processes in order to conform to the tool. This can lead to a loss of flexibility and a failure to truly tailor the tool to the individual needs of the business. Finally, using a common TQM tool can also lead to a loss of control. If a business is using a tool that is not under their direct control, they may be at the mercy of the tool's creator in terms of updates, changes, and support.
Check this out: Which of the following Is Not a Form of Light?
How does a common tqm tool help improve quality?
There are many tools available to help organizations improve quality. One common tool is known as Total Quality Management, or TQM. TQM is a system that focuses on continuous improvement of all aspects of an organization. It includes elements such as quality planning, quality control, and quality improvement.
TQM can help organizations improve quality in a number of ways. One way is by promoting communication and collaboration among employees. TQM encourages employees to work together to identify and solve problems. This can help to prevent quality issues from occurring in the first place.
Another way TQM can help improve quality is by promoting a culture of continuous improvement. TQM encourages employees to identify areas where improvements can be made. This can help to ensure that quality issues are quickly identified and corrected.
Finally, TQM can help improve quality by providing employees with the tools and training they need to do their jobs effectively. TQM provides employees with the skills they need to identify and solve quality issues. It also gives employees the ability to track progress and measure results. This can help to ensure that quality improvements are made on an ongoing basis.
In summary, TQM is a system that can help organizations improve quality in a number of ways. It promotes communication and collaboration among employees, encourages a culture of continuous improvement, and provides employees with the tools and training they need to do their jobs effectively.
What are some of the most popular tqm tools?
There are a variety of quality management tools available to organizations. Some of the most popular tools include:
1. Benchmarking: Comparing organizational performance against other similar organizations in order to identify best practices and areas for improvement.
2. Process mapping: Visually depicting the steps and activities involved in a process in order to identify inefficiencies and potential improvements.
3. cause and effect diagrams: Also known as fishbone or Ishikawa diagrams, these tools are used to identify potential causes of problems or defects in a process.
4. Control charts: Used to monitor process performance over time, control charts can help identify trends and potential issues.
5. Pareto charts: Used to identify the most important factors in a process or problem, Pareto charts can help prioritize improvement efforts.
6. Historical data analysis: Examining past performance data can help identify patterns and trends that can be used to predict future behavior.
7. Seven basic quality tools: Often used in manufacturing, these tools include cause and effect diagrams, control charts, histograms, Pareto diagrams, scatter plots, and fishbone diagrams.
8. Statistical process control (SPC): A statistical approach to quality management that uses statistical techniques to monitor and control process variation.
9. Total quality management (TQM): An approach to quality management that emphasizes continuous improvement and the involvement of all employees in the organization.
10. Six Sigma: A methodology for process improvement that emphasizes the use of statistical tools and techniques to achieve near-perfection in a process.
What industries benefit most from using tqm tools?
Quality management tools are essential for any organization that wishes to improve its performance. By definition, quality management is "a strategic approach to managing organizations that focuses on continuous improvement of organizational processes and products, with the overall goal of reducing costs and improving customer satisfaction" (ASQ, 2018). Although quality management tools were originally developed for manufacturing organizations, they are now commonly used in service-based industries as well.
There are many different quality management tools available, and the specific tools that are most beneficial to an organization depend on the specific industry and organizational needs. However, some quality management tools are more commonly used than others and tend to be beneficial across a wide range of industries. These tools include process mapping, statistical process control, cause-and-effect diagrams, and fishbone diagrams.
Process mapping is a quality management tool that can be used to visualize and improve organizational processes. Process mapping allows organizations to see the "big picture" of their process and identify potential areas of improvement. For example, a manufacturing organization might use process mapping to identify bottlenecks in its production line. By identifying these bottlenecks, the organization can make changes to its process to improve efficiency.
Statistical process control is another quality management tool that is commonly used in manufacturing and service industries. Statistical process control involves using statistical techniques to monitor and control process-related variables. For example, a manufacturing organization might use statistical process control to monitor the dimensions of its products. By doing so, the organization can ensure that its products meet customer specifications.
Cause-and-effect diagrams and fishbone diagrams are two quality management tools that are often used together. Cause-and-effect diagrams are used to identify the potential causes of a problem, while fishbone diagrams are used to identify the potential root causes of a problem. For example, if a customer complains about a defective product, a cause-and-effect diagram could be used to identify the potential causes of the defect (e.g., a problem with the manufacturing process, a problem with the design of the product, or a problem with the materials used to make the product). Once the potential causes of the problem have been identified, a fishbone diagram could be used to identify the root cause of the problem.
In summary, quality management tools are beneficial for any organization that wishes to improve its performance. There are many different quality management tools available, and the specific tools that are most beneficial to an organization depend
What is the difference between a common tqm tool and other quality management tools?
There are many tools available to quality managers in order to help them improve the quality of their organizations' products and services. However, not all of these tools are created equal. Some, like common tqm tools, are more widely used and have been shown to be effective in many different settings. Others, like Six Sigma and lean management, are more specialized and may be more appropriate for certain organizations or projects.
So, what is the difference between a common tqm tool and other quality management tools? Simply put, common tqm tools are those that are more widely used and have been shown to be effective in a variety of settings. Six Sigma and lean management, on the other hand, are more specialized tools that may be better suited for certain organizations or projects.
There are a number of reasons why common tqm tools are more widely used than other quality management tools. First, they tend to be less expensive. This is because they are generally less complex and require less training to use effectively. Second, common tqm tools are usually more flexible than other quality management tools. This means that they can be adapted to fit the specific needs of any given organization.
Finally, common tqm tools have a proven track record. This is because they have been used successfully in a variety of settings and have a long history of producing results. In contrast, many other quality management tools are still relatively new and have not yet been widely used or tested.
While common tqm tools may be less expensive, more flexible, and have a proven track record, they are not necessarily the best choice for every organization. In some cases, other quality management tools may be more appropriate. For example, if an organization is seeking to implement a very specific and complex quality management system, it may be better off using a tool like Six Sigma. Similarly, if an organization is looking to improve its overall product or service quality, lean management may be a better choice.
Ultimately, the decision of which quality management tool to use depends on the specific needs of the organization. Common tqm tools are generally a good choice for most organizations, but there may be cases where other quality management tools are more appropriate.
Take a look at this: Effective Tool
How do I select the right tqm tool for my organization?
There is no single answer to this question, as the appropriate TQM tool(s) for an organization depends on numerous factors specific to that organization. However, there are some general guidelines that can be followed in order to select the most appropriate TQM tool(s) for an organization.
First and foremost, it is important to assess the specific needs of the organization in terms of quality improvement. What are the organization's goals and objectives in terms of quality? What areas of the organization's quality system need to be improved? Once the organization's specific needs have been identified, it is then possible to begin identifying which TQM tools would be most appropriate for addressing those needs.
There are a variety of different TQM tools available, each of which can be used to improve different aspects of an organization's quality system. Some of the more common TQM tools include quality circles, process mapping, process improvement teams, control charts, andTotal Quality Management (TQM) software. It is important to select TQM tools that will be most effective in addressing the specific needs of the organization. For example, if the organization's goal is to improve communication and collaboration among employees, quality circles would be a more appropriate tool than control charts.
Once the specific needs of the organization have been identified and the most appropriate TQM tools have been selected, it is important to ensure that the chosen tools are properly implemented. TQM tools are only effective if they are used correctly and consistently. Training may be necessary to ensure that employees understand how to properly use the selected TQM tools. Furthermore, it is important to establish measurable goals and objectives for the implementation of TQM tools so that progress can be monitored and quality improvements can be documented.
Selecting the right TQM tool(s) for an organization is a critical step in ensuring the success of a quality improvement initiative. By carefully assessing the specific needs of the organization and selecting the most appropriate TQM tools, organizations can improve their quality systems and ultimately achieve their quality goals.
How do I implement a common tqm tool in my organization?
There is no single answer to this question as it depends on the specific organization and what common tqm tools are available. However, some tips on how to implement a common tqm tool in an organization include:
1. first, assess the needs of the organization and the specific tqm tools that would be most beneficial.
2. Next, develop a plan for implementing the chosen tqm tool.
3. Then, train employees on how to use the tool and make sure they are familiar with its purpose and how it works.
4. Finally, monitor the implementation of the tool to ensure it is being used effectively and making a positive impact on the organization.
Frequently Asked Questions
What are TQM tools that management can use in Total Quality Management?
1. TQM Tools for Analysis -Tool for analysis can help measure the improvement in product quality, process flows and work areas. -It also helps to identify where improvement is needed in order to reduce process variation and decrease the amount of rework and customer complaints. -The tool can be used by quality management teams, production engineers or managers responsible for specific aspects of product quality, process flow or work area. 2. TQM Tools for Improvement -Tool for Improvement helps managers to identify where they need to focus their efforts to improve total quality in their organization. -It provides a structured approach that allows managers to measure performance against results expectations, identifies root causes of defects and makes necessary changes. 3. TQM Tools for Communication -Tool for Communication supports communication between team members and trainers/educators working on improving total quality within an organization. -It facilitates effective sharing of learning materials, techniques and successes so
What are the advantages and disadvantages of TQM?
Advantages of TQM include the following: 1. Cost reduction. When applied consistently over time, TQM can reduce costs throughout an organization, especially in the areas of scrap, rework, field service, and warranty cost reduction. Disadvantages may be that some individuals in the organization may feel that they are micromanaged or not able to make decisions on their own. 2. Productivity improvement. In many cases, TQM programs result in increased levels of productivity than traditional methods. This is due to the teamwork approach adopted by TQM proponents and the tight harmonization betweenprocesses and products resulting from total quality control measures. However, this benefit depends largely on the characteristics of the organization and its work force, so it cannot be taken for granted. 3. Customer satisfaction. In general, customers tend to be more satisfied with products and services that meet or exceed their expectations as a result of effective TQM implementation. However, there are some limitations
What are the benefits of Total Quality Management?
The benefits of total quality management are many and vary depending on the company and what is being improved. However, some general benefits include: Improved processes and products Reduced error rates Improved customer satisfaction Better communication and collaboration between employees and business partners
How can TQM help business schools?
There is no one answer to this question, as the impact of TQM on business schools depends on the specific school and its goals. However, some possible benefits of using TQM principles in business schools include increased productivity, better quality control, and a reduction in waste. Additionally, using TQM can help businesses improve their communication processes so that they can more effectively collaborate with other entities.
What is TQM tools?
TQM tools is a term referring to all sorts of management tools that can be used to improve an organization's overall process, productivity and efficiency. This includes things like formal organizational structures and processes, as well as human resources systems and training programs. TQM tools are often targeted at all employees in the organization, not just those in strategic leadership positions.
Sources
- https://www.educba.com/tqm-tools/
- https://www.chegg.com/homework-help/questions-and-answers/following-common-tqm-tool-o--scatter-diagrams-ob-check-sheets-oc-histograms-od-queuing-mod-q88736418
- https://howandwhat.net/advantages-disadvantages-total-quality-management-tqm/
- https://oneclass.com/homework-help/management/5575105-which-of-the-following-is-not-a.en.html
- https://knowledgeburrow.com/what-are-the-tqm-techniques/
- https://iosfuzhu.com/how-does-tqm-improve-quality/
- https://www.coursehero.com/file/p776q9f/Which-of-the-following-is-NOT-a-common-TQM-tool-A-scatter-diagrams-B-queuing/
- https://quizlet.com/125831368/chapter-6-questions-flash-cards/
- https://www.coursehero.com/file/p113cbde/16-Which-of-the-following-is-NOT-a-common-TQM-tool-A-queuing-models-B-histograms/
- https://bizfluent.com/info-8201247-advantages-disadvantages-tqm.html
- https://www.educba.com/total-quality-management-benefits/
- https://oshmusic.com/articles/what-are-the-benefits-of-using-tqm
- https://www.bartleby.com/questions-and-answers/which-of-the-following-is-not-a-common-strategic-compensation-goal-o-to-control-employees-exiting-th/67cbcf3f-6a1b-4144-8b1b-7879f7052906
- https://quizlet.com/344674350/ops-301-rq-10-flash-cards/
Featured Images: pexels.com