
Creating architectural cardboard models is a fun and creative process that brings building designs to life.
Cardboard models can be made from a variety of materials, including corrugated cardboard, chipboard, and even cereal boxes.
These materials are often readily available and inexpensive, making them a great choice for model makers.
From concept to reality, cardboard models can be scaled up or down to represent buildings of any size.
The process of creating a cardboard model typically begins with sketching out a design or blueprint of the building.
This helps model makers visualize the structure and identify potential issues before starting construction.
By using cardboard as the primary material, model makers can create highly detailed and textured models that showcase the building's features.
If this caught your attention, see: Sustainable Building Design
Types and Materials
Card materials are incredibly versatile and widely used in architectural cardboard models. They come in many different color options and finishes.
Their unique combination of thickness and rigidity, along with flexibility, makes them perfect for crafting detailed and sturdy models. Card materials remain just as flexible to work with as paper, allowing for precise cuts and folds.
Their huge variety and availability make them a go-to choice for many model makers, and for good reason - they're easy to work with and can produce impressive results.
Expand your knowledge: Green Architecture Materials
What Are the Types?
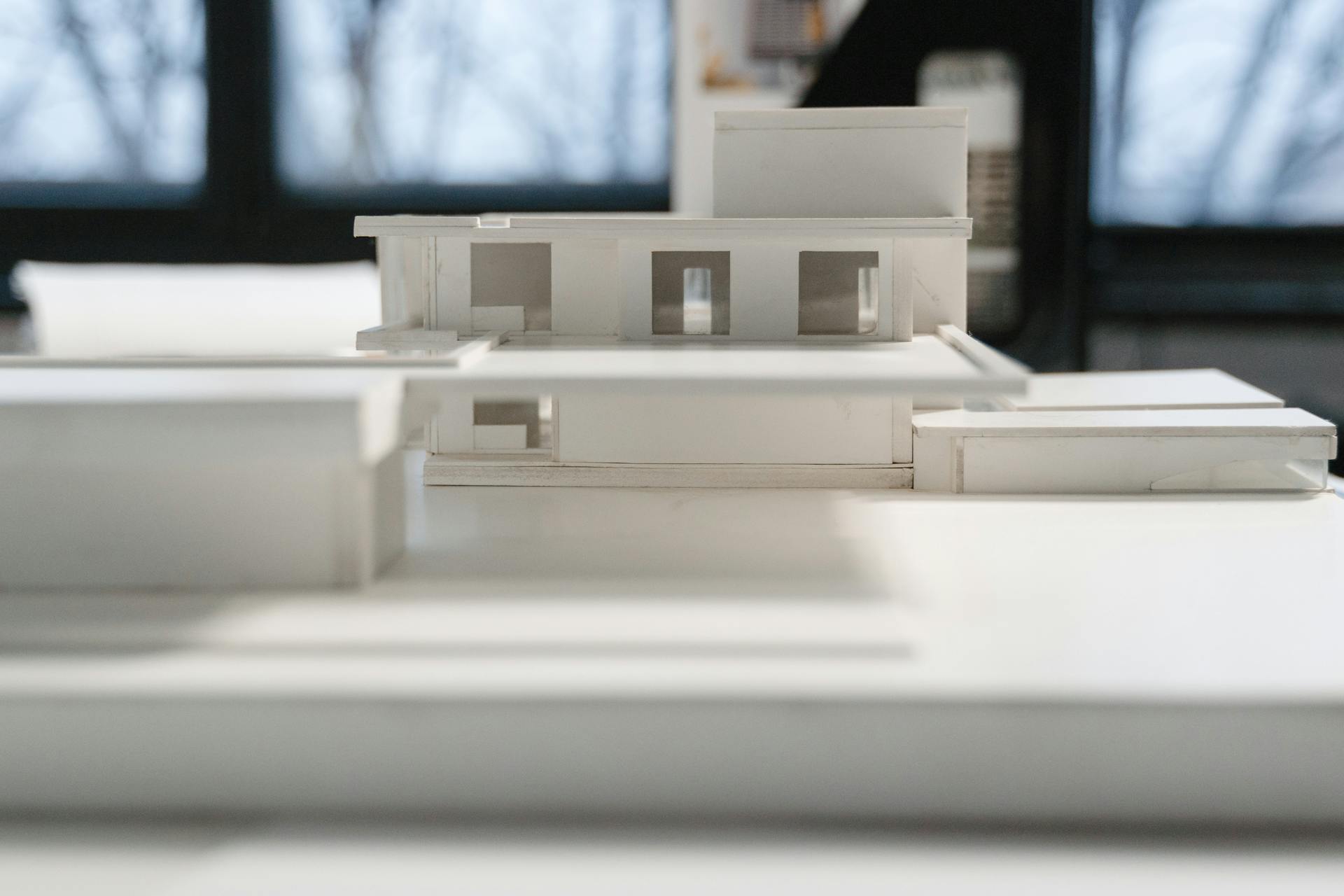
There are several types of materials used in construction, including wood, steel, and concrete.
Wood is a popular choice for framing and finishing work due to its cost-effectiveness and versatility.
Steel is commonly used for structural elements, such as beams and columns, because of its high strength-to-weight ratio.
Concrete is often used for foundations, walls, and floors due to its durability and ability to withstand heavy loads.
Some materials are more suitable for specific applications, such as wood for interior finishing work or steel for high-rise buildings.
Steel framing is also used in some residential construction due to its speed of assembly and energy efficiency.
A fresh viewpoint: Green Roofing and Construction
Paper
Paper is a popular choice for architecture model-making due to its inexpensiveness.
It's easy to cut and manipulate, making it perfect for quick volume studies and conceptual models.
Paper materials are often used for initial model-making stages because of their flexibility.
This allows architects to experiment and refine their ideas without breaking the bank.
Card
Card is a versatile material that offers a wide range of color options and finishes.
It's much thicker and more rigid than paper, yet still flexible to work with.
This combination of properties makes card a go-to choice for many applications.
Card is one of the most widely used materials due to its huge variety and availability.
Corrugated
Corrugated cardboard is one of the most easily sourced architecture model materials, often available for free. It's excellent for initial study models, and can also provide a good model base.
You can get a finer grain corrugated cardboard that can provide the effect of corrugated metal sheets.
Benefits of Making Physical Things
Making physical architectural models has numerous benefits, and I'm excited to share them with you. Physical models can give a sense of scale and help the client envision what the built space would look like.
Spatial understanding is greatly improved with physical models, allowing clients to see different angles and perspectives. This tactile experience can be used to keep the client engaged and interested.
Physical models are also awesome for testing out ideas, offering a more flexible way of getting ideas out and helping the creative process to flow. This is especially true for complex designs that require multiple iterations.
Here are some key benefits of making physical architectural models:
- Representation of different materials: Different materials can mimic the real-world materials that will be used in the actual building.
- Texture and aesthetics: Different materials bring different textures and aesthetics to a model.
- Structural properties: Some materials are sturdier than others, providing the necessary rigidity and support for a model.
- Level of detail: High-quality materials, such as museum board, can be used to craft finely detailed presentation models.
- Cost and availability: Budgetary constraints can influence material choice, with more affordable materials preferred for quick iterations or study models.
- Ease of manipulation: Some materials are easier to cut, shape, and join than others, depending on the design complexity.
- Transparency and lighting studies: Materials like vellum or clear acetate can be used to simulate transparent building elements.
- Layering and depth: Different materials can be layered to create depth and emphasize the stratification or hierarchy of spaces within a design.
- Scale: The scale of the model can dictate the type of material used.
- Audience and presentation: The intended audience or context of presentation might influence material choice.
Physical models can be used to facilitate project presentation, prevent construction problems, and assist in fundraising. They can also be used for client communication, sales and marketing, public information, planning, education and research.
In short, making physical architectural models is a great way to communicate design ideas, test out ideas, and collaborate with clients and team members.
Design and Creation
Architectural cardboard models are a great way to visualize and communicate design ideas. With the right tools and techniques, you can create precise and detailed models that will help you bring your vision to life.
To create an effective architectural model, consider the scale, tool selection, construction sequence, aesthetic presentation, and budget-friendly strategies. These factors will help you elevate your model to the best of its potential.
For cutting and assembling your model, you'll need the right tools. A stainless steel wheel-locked utility knife with replaceable blades is a great choice for clean, neat cuts. Precision knives are also ideal for intricate details, as they are exceedingly sharp, durable, and easy to maintain.
A self-healing cutting mat is essential for protecting your cutting blades and workspace. You can also use laser cutting for precision and clean edges, but it may require more investment.
For assembly, you'll need adhesives such as glue sticks, wood glue, and double-sided tape. A glue syringe can be useful for applying adhesives neatly and precisely.
Here are some tools you may consider for cutting and assembling your architectural cardboard model:
- Utility knife with replaceable blades
- Precision knife
- Scissors (preferably with a comfortable grip)
- L-Square for drawing perpendicular lines
- Metal rulers (6", 12", and 18") for straight cuts
- Self-healing cutting mat
- Laser cutting (for precision and clean edges)
- Glue sticks
- Wood glue
- Double-sided tape
- Glue syringe
Using these tools and techniques, you can create a precise and detailed architectural cardboard model that will help you communicate your design ideas effectively.
Design and Creation (continued)
Creating an architectural model can be a detailed and intricate process, but with the right tools and strategies, you can elevate your model to the best of its potential.
In film and television production, set designers use to-scale miniature models to visualize their designs. These models are often created using white mat board, which provides a precise and detailed representation of the intended design.
The white card model is a three-dimensional blueprint of the set design, incorporating technical drawings and precise details. It's a crucial step in the design process, providing a clear understanding of how each part is meant to go together.
Laser cutting is a great option for building architectural models, offering precision cuts, detailed engraving, and speed of production. This method is particularly useful for creating intricate designs and complex models.
Tom Houha, an architect and designer, uses laser cutting to create 3D models that he gives as gifts to family and friends. His interest in geometry and building models has led to a successful business, producing his designs commercially.
Here are some alternative design and creation methods to consider:
- Laser Cutting
- Laser Engraving
- Photo Etching
- Promotional Products
- 3D Printing Alternative
Tools and Techniques
Choosing the right tools is crucial for creating a high-quality architectural cardboard model. A stainless steel wheel-locked utility knife with replaceable blades is highly recommended for clean, neat cuts.
Precision is key when cutting cardboard, and tools like precision knives, scissors, and metal rulers can help achieve this. Scissors with a comfortable grip are ideal for fine details, while a self-healing cutting mat protects your cutting blades and workspace.
For assembly, consider using glue sticks, wood glue, or double-sided tape, depending on the materials and project requirements. Be careful when using double-sided tape with card or paper, as it can tear away if removed.
A glue syringe can also be useful for applying adhesives with precision, and straight pins can hold pieces together temporarily while the glue sets.
Expand your knowledge: Architectural Tools for Drafting
The Role of Physical
Physical models are a powerful tool in the world of architecture and design. They provide a tactile and interactive experience that can help clients envision what a built space will look like.
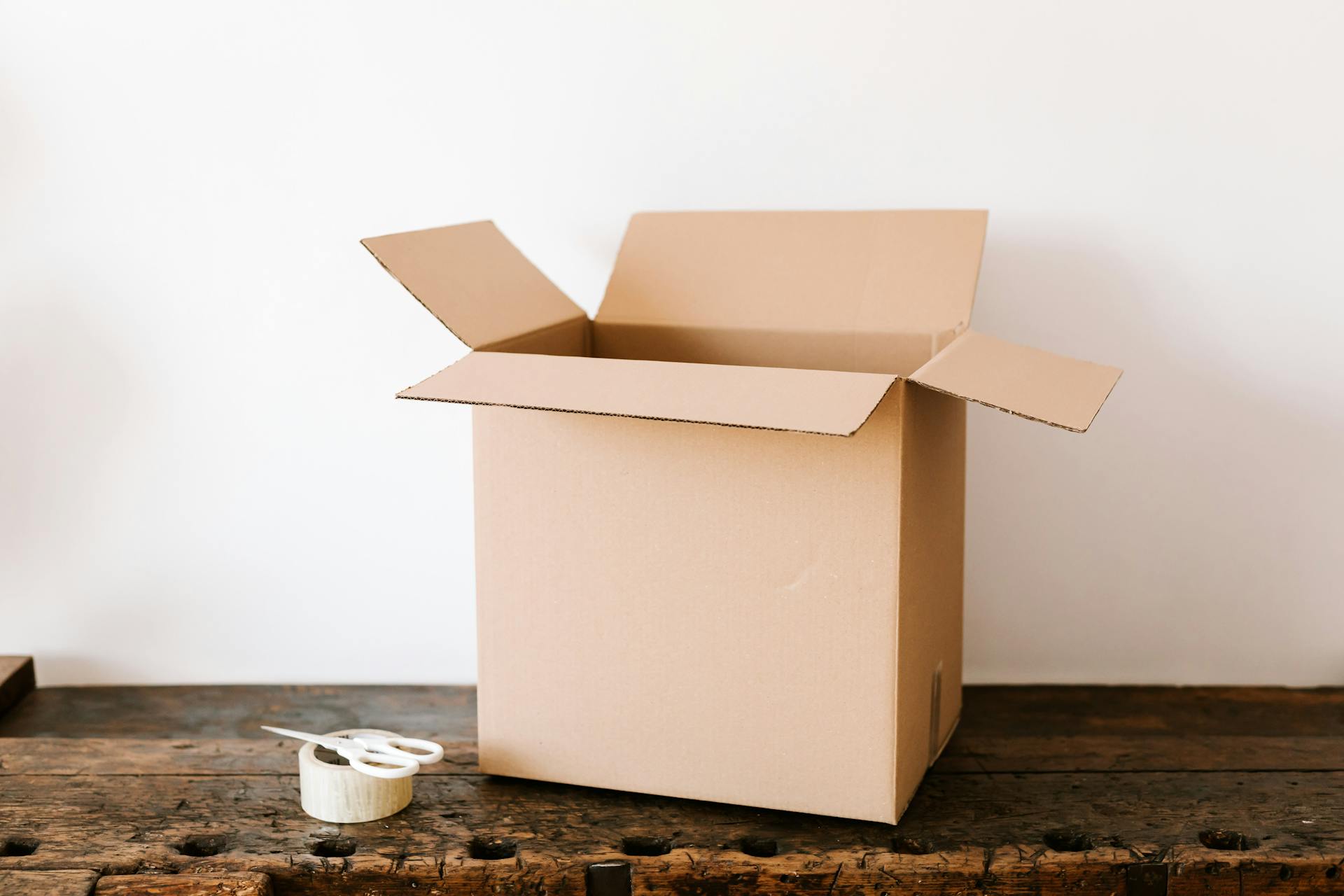
By creating a physical model, architects and designers can give clients a sense of scale and proportion, which is essential for understanding how different spaces connect with each other.
Physical models can be used to test out ideas and iterate on designs, making the creative process more flexible and effective.
They can also be used to highlight design elements and help clients build a deeper understanding of the project.
Physical models can be used to identify potential design flaws and issues that may arise during the construction phase, saving time and resources in the long run.
Collaboration is key in the design process, and physical models can be used by teams to generate ideas and refine details in a collaborative manner.
Material exploration is also an important aspect of physical modeling, allowing designers to experiment with different materials and finishes.
In the film and television industry, set designers use to-scale miniature models to bring their designs to life. These models are often made using laser cutting and engraving techniques, which provide precision and detail.
Physical models can be used for fundraising purposes, providing investors with a tangible visualization of the project and how their investment will be utilized.
You might enjoy: Architectural Design Process Diagram
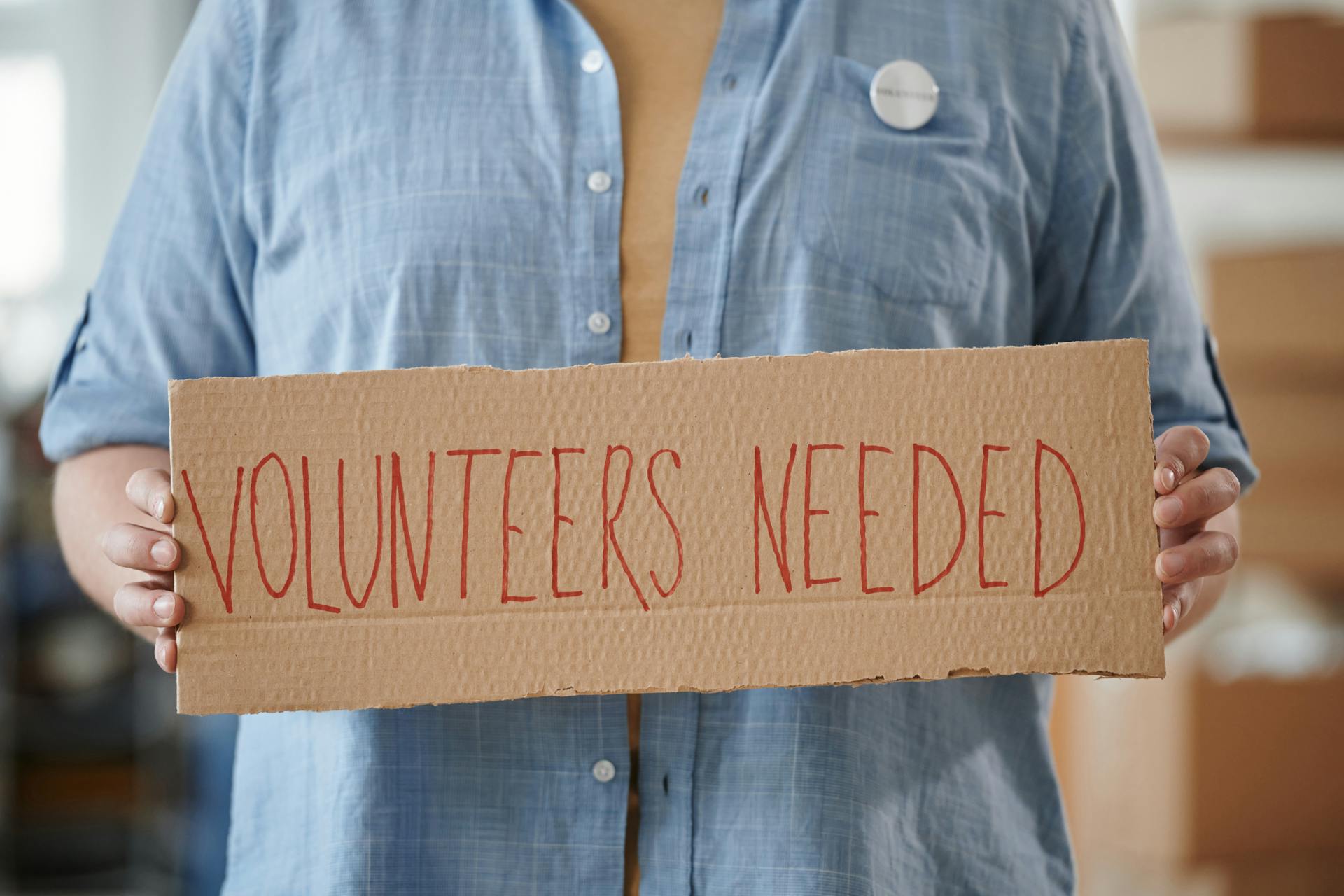
In fact, a well-crafted physical model can serve as an effective tool in raising funds for a project, allowing investors to see exactly how their investment will be used.
Here are some of the key benefits of using physical models in the design process:
- Facilitating project presentation
- Preventing construction problems
- Assisting in fundraising
By incorporating physical models into the design process, architects and designers can create more effective and engaging projects that meet the needs of their clients.
Choosing the Right Tools for Cutting and Assembly
A stainless steel wheel-locked utility knife with replaceable blades is highly recommended for clean, neat cuts.
Precision knives are exceedingly sharp, durable, and easy to maintain, making them ideal for intricate details.
Small titanium scissors can be used for fine details, but it's essential to opt for scissors with a comfortable grip to avoid discomfort during prolonged use.
A stainless steel L-square can help you draw perpendicular lines accurately and swiftly, and attaching masking tape to the back of the L-square can provide added stability.
Having 6″, 12″, and 18″ metal rulers at hand can be beneficial for achieving straight cuts, depending on the size of your model.
A self-healing cutting mat can protect your cutting blades from premature dulling and prevent damage to your workspace.
If you're unsure about your cutting abilities or willing to invest more for precision, laser cutting could be an option, where you design the components on a program like AutoCAD, and the laser cutter handles the cutting process.
For assembly, glue sticks are a low-cost and easy-to-use option, but the adhesive strength isn't very high, making them most effective with paper and not producing long-lasting results.
Wood glue is a must for models involving wooden components, and it's essential to wipe away any excess immediately as it can leave stains.
Double-sided tape is strong, clean, and adjustable, but be careful with placement because attempting to remove it after application can damage paper or foam board surfaces.
Straight pins can be used to hold pieces together temporarily while the glue sets.
Acrylic resin glue is a very fast-acting glue, but it's not suitable for paper or card, and care needs to be taken when using it.
Wood glue is suitable for card, foam, and paper, but not for metal or plastic.
PVA is an all-purpose glue that works well with card, paper, and foam board, but it's not as strong as wood glue.
Solvent-based glue is best for materials like clear acrylic, where you want the glue to dry clear and leave no residue.
Clear synthetic resin, like UHU, dries clear and is suitable for paper, card, and foam.
Spray mount is a sprayable glue that makes for easy fixing of card onto card, but it can get everywhere, so be careful where it's used.
Additional reading: Architectural Wood Models
Digital Methods
Digital methods have revolutionized the way we create physical models, allowing for faster prototyping and design exploration. With technology advancing at a rapid pace, you can now take your virtual 3D models and convert them into physical ones.
Laser cutting is a game-changer for architects and students, enabling accurate and quick cutting of various materials like wood, cardboard, paper, foam, polystyrene, and acrylics. The preparation required involves developing a CAD drawing for the laser cutting machine, which can be done using a 2D CAD drawing to lay out the pieces of the puzzle.
Curious to learn more? Check out: Architectural Drawings Cad
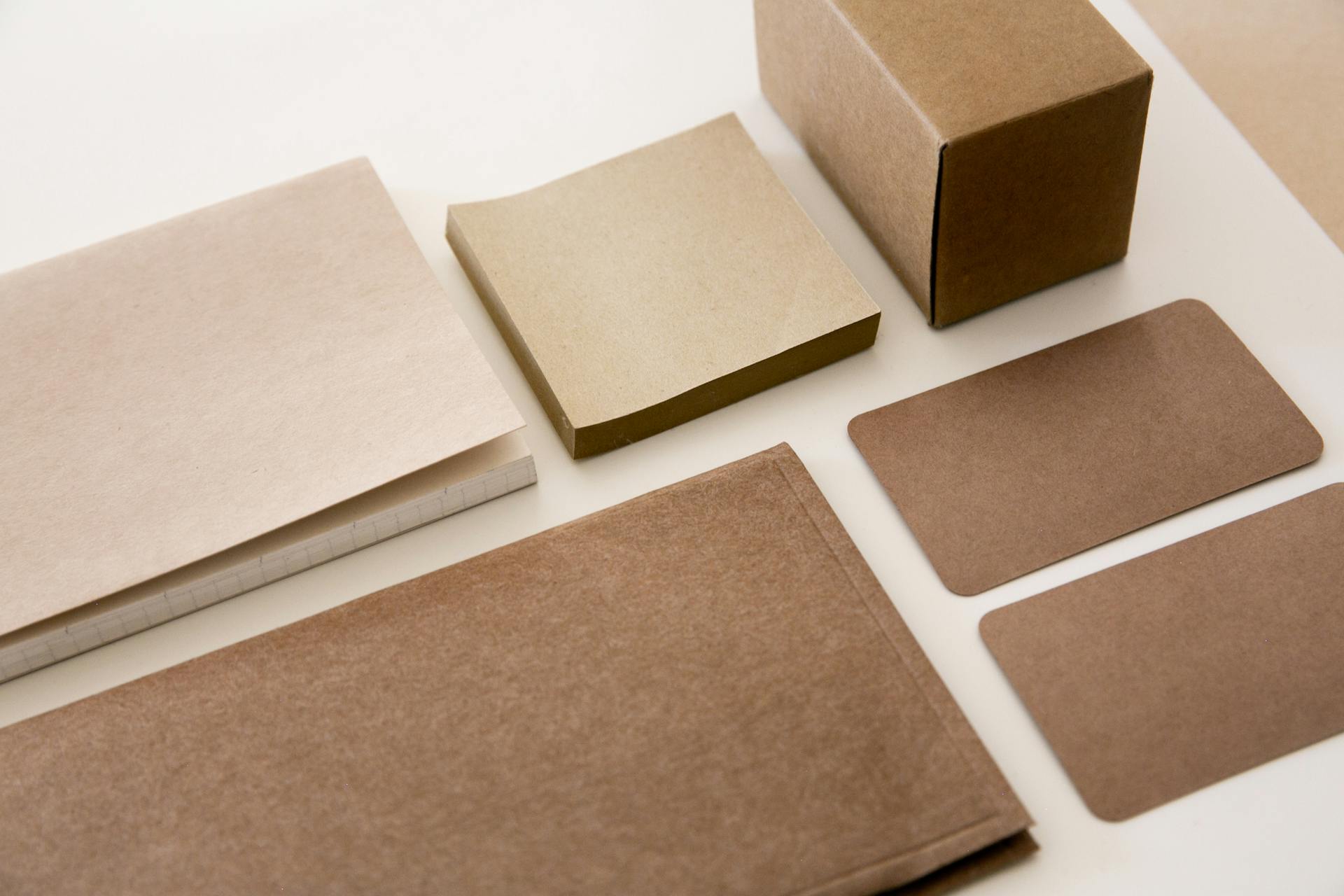
For a more in-depth look at laser cutting, check out the tutorial on Instructables, which walks you through the process of preparing your design for laser cutting. This resource is a great starting point for those new to laser cutting.
3D printing is another exciting digital method that has been adopted by professional model makers, providing clients with fast, accurate, and cost-effective models. The output is clean and contemporary, extracted from CAD.
The video demonstrating 3D printing and finishes is worth watching, showcasing the types of 3D printing and finishes that can be obtained. This is a great way to see the capabilities of 3D printing up close.
Consider reading: Great Architectural Drawings
Frequently Asked Questions
Who is the architect who uses cardboard?
Ban is a pioneering architect known for using innovative materials like paper and cardboard tubing in his designs. He was the first in Japan to build a house primarily out of paper, requiring special approval to meet building codes.
What is a cardboard model called?
Cardboard models are also known as paper models or papercraft. They are constructed from heavy paper, paperboard, card stock, or foam.
Sources
- https://www.lifeofanarchitect.com/a-case-for-building-architectural-models/
- https://www.firstinarchitecture.co.uk/architectural-model-making-the-guide/
- https://www.archisoup.com/architectural-model-making-equipment
- https://www.ponoko.com/blog/materials/building-architectural-models-prototypes/
- https://commonedge.org/maquettes-in-architecture-the-forgotten-joys-of-model-making/
Featured Images: pexels.com