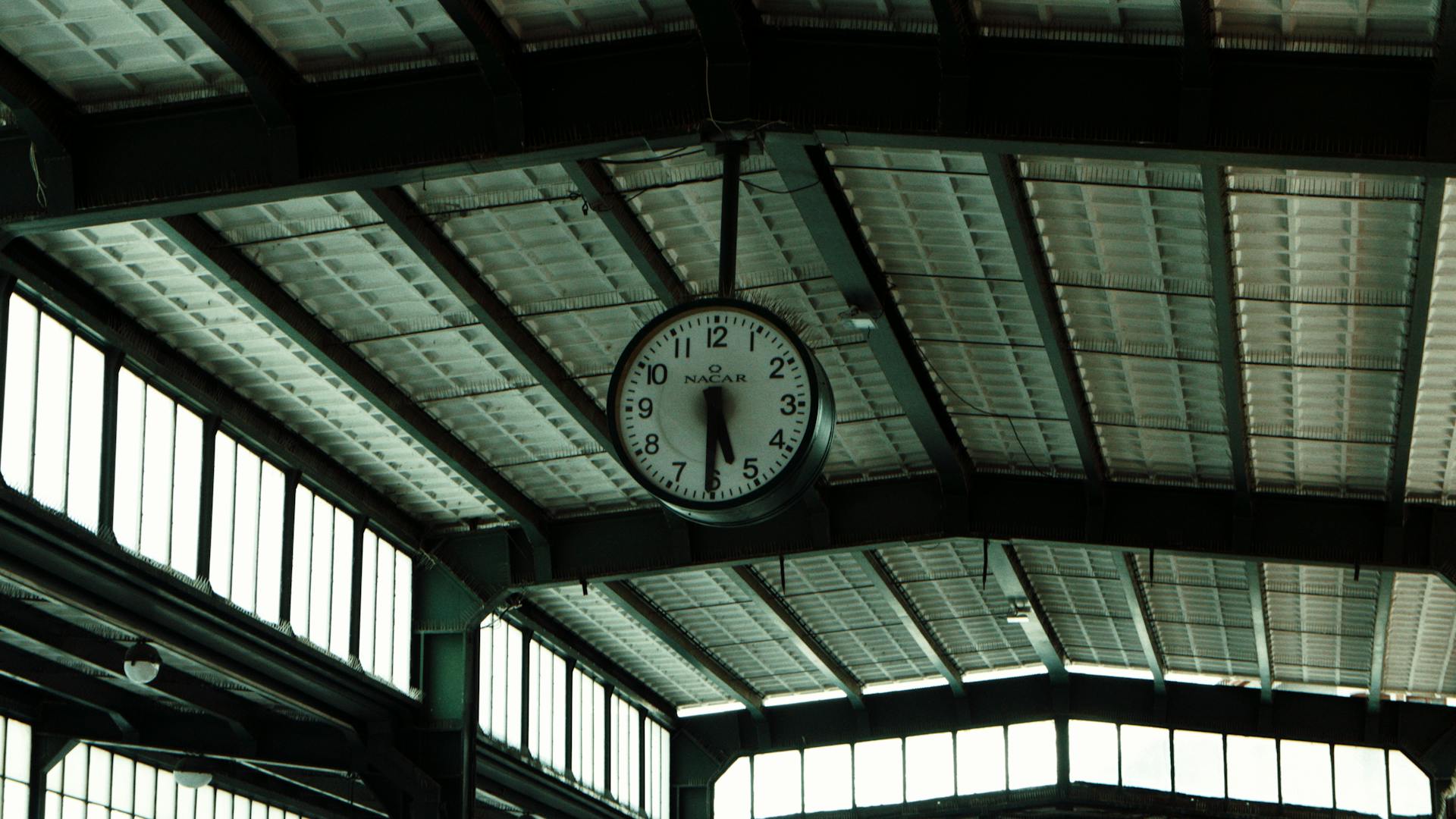
C purlins are a crucial component of many roof designs, providing a sturdy and efficient way to support roofing materials. They can be used in a variety of applications, from residential to commercial buildings.
A key benefit of c purlins is their ability to reduce the number of roof beams required, making them a cost-effective option. By using c purlins, builders can save on materials and labor costs.
C purlins are typically made from steel or aluminum and come in a range of sizes and gauges. The choice of material and size will depend on the specific design requirements and load-bearing capacity needed.
A unique perspective: Commercial Roof Materials
What Is C Purlin Roof Design?
A C purlin roof design is a type of roof structure that uses C-shaped metal purlins to provide support and stability. C purlins are commonly used in building construction, particularly in commercial and industrial buildings.
C purlins are typically made of metal, such as steel or hot-dipped galvanized steel, and come in various gauges, including 12 ga, 14 ga, and 16 ga. They are available in different sizes, ranging from 4” to 12” in width.
In a C purlin roof design, the C purlins are placed perpendicular to the roof framing members, such as rafters or trusses, and serve as supporting structures, distributing the load of the roof to the main structural elements. This design provides excellent structural support and allows for greater design flexibility.
The C purlins can be finished in various ways, including Red Oxide or Galvanized, which provides a durable and long-lasting finish.
Additional reading: How to Install C Purlins
Types and Options
C-purlins are a popular choice for construction projects due to their versatility in accommodating various sizes and thicknesses.
Their "C" shape and flanges on each side provide effective load transfer and stability, making them suitable for multiple projects.
C-purlins are commonly chosen for applications where stability is paramount.
In contrast, Z-purlins offer heightened structural strength and secure attachment to rafters or trusses, thanks to their "Z" shape and ridges.
The choice between C-purlins and Z-purlins ultimately depends on the required load-bearing capacity, the desired level of structural stability, and the architectural preferences of the project.
A fresh viewpoint: Roof Form
What Are the Types of C Purlins
C purlins come in various shapes and are typically made of metal, such as steel, aluminum, or hot-dipped galvanized steel.
Our metal purlins are commonly used in commercial and industrial buildings and in some residential metal roofs.
C purlins are a type of metal purlin that provides excellent structural support, allowing for greater design flexibility and the ability to span long distances without the need for supporting columns or beams.
They are lightweight yet sturdy, making them cost-effective and easy to handle during installation.
Z-Options
Z purlins are a great choice for buildings with large roof slopes, as they can support heavy structures and are extremely strong.
They're commonly used in agricultural and industrial buildings, where a bigger roofing or loading capacity is required.
Z purlins can be overlapped continuously, making them ideal for metal buildings with longer spans.
This feature also allows them to be used for a variety of purposes, including supporting beams required for flooring.
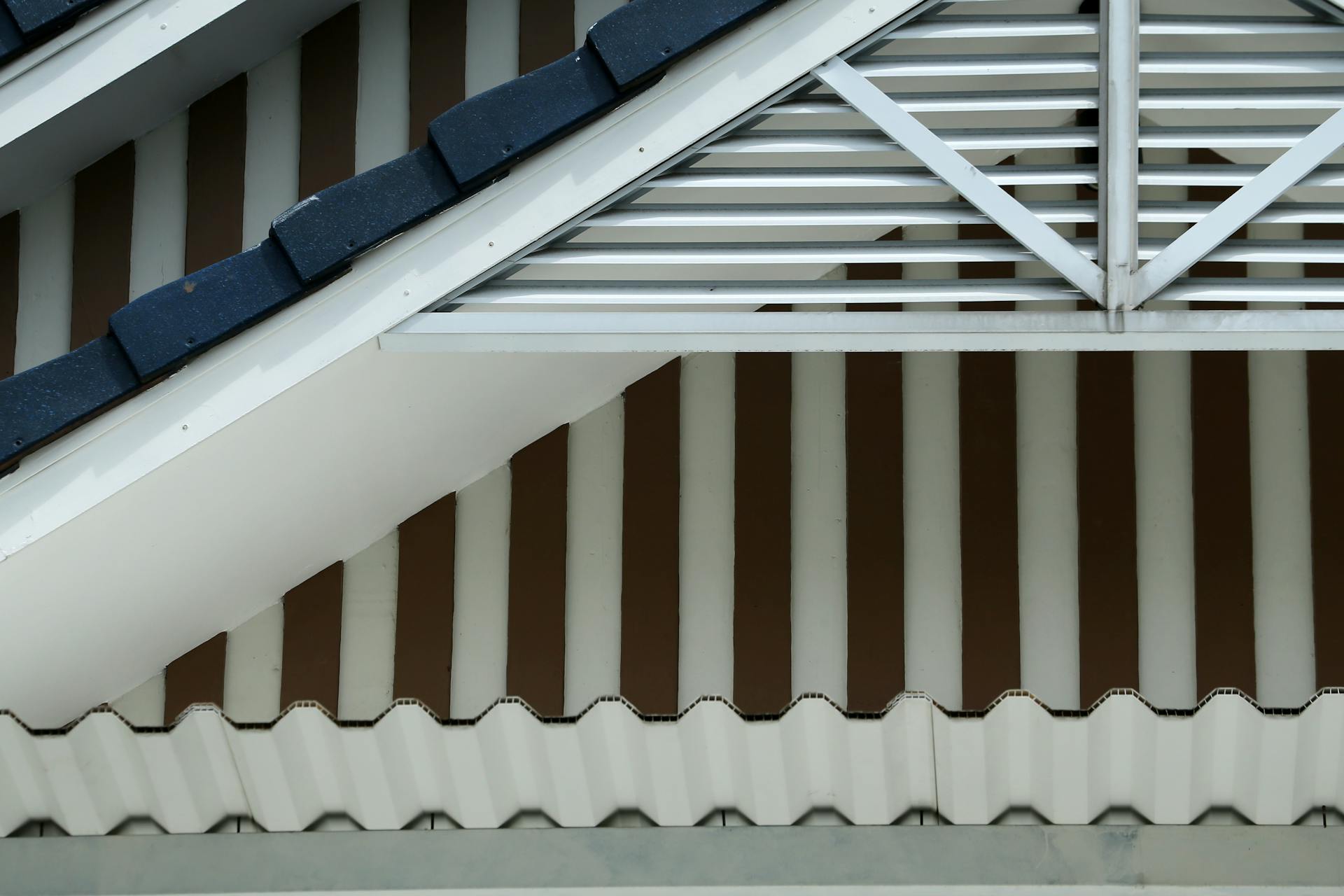
Z purlins usually sit between roofing sheets to provide support, and are a better choice for buildings with large slopes.
They're also more flexible than C purlins, with an angle that's less than 90 degrees, making them a great option for projects that require a high level of structural stability.
Z purlins are typically used in commercial and industrial buildings, as well as some residential metal roofs, where their lightweight yet sturdy nature is beneficial.
They offer several advantages, including their durability and ability to provide excellent structural support, allowing for greater design flexibility.
Additional reading: How to Support Roof Purlins
Sizes
Purlins come in a range of sizes to suit different construction needs. Typically, they measure anywhere from 4” up to 12” with a flange width of 1-½” up to 4”. Custom sizes and lengths are available for specific projects.
The most common sizes for purlins are diverse and versatile, catering to various construction needs. They are offered in various dimensions, including 12g (up to 21 inches), 14g (up to 24 inches), and 16g (up to 16 inches).
These different sizes allow for flexibility in accommodating different structural requirements.
Discover more: Zed Purlins Sizes
Gauges
Metal purlins come in a range of gauges, including 12 gauge, 14 gauge, and 16 gauge.
The most common gauges are 12 gauge, 14 gauge, and 16 gauge.
Each gauge has its unique strength and load-bearing capabilities, making it essential to select the most suitable gauge for optimal structural support.
Consult with your engineer to determine which gauge is best for your project, as they can assess your specific needs and recommend the right gauge.
Materials and Finishing
Red oxide and galvanized are the two common finishes for metal purlins, with red oxide consisting of a sprayed paint primer in a red finish and galvanized being a zinc-alloy plating that provides corrosion resistance.
Galvanized metal purlins are ideal for harsh environments, such as coastal areas, where exposure to saltwater would otherwise lead to rusting in unfinished steel.
Red oxide purlins, on the other hand, are best suited for projects where a top coat of paint will be applied, as the red primer prepares the steel for painting.
Expand your knowledge: Steel Roof Truss Design Example
Galvanized purlins are more corrosion-resistant, but they're also more difficult to paint compared to red oxide primers.
The cost of galvanized purlins is higher, but they can last longer than red oxide purlins, especially in corrosive environments.
Here's a comparison of the two finishes:
Galvanized
Galvanized metal purlins are a great choice for construction projects that require maximum durability and corrosion resistance. They're perfect for harsh environments like chemical plants or coastal areas where saltwater exposure would otherwise lead to rusting in unfinished steel.
The galvanization process involves applying zinc-alloy plating to the metal, creating a protective barrier against corrosion. This makes galvanized purlins ideal for projects requiring long-lasting support near the ocean or in other corrosive environments.
Galvanized steel is not entirely immune to oxidation and may develop white rust when exposed to moisture, but it still outperforms non-galvanized alternatives in longevity and resilience. In fact, it's the optimal choice for projects that need to withstand harsh conditions.
Galvanized purlins will cost more money compared to red oxide purlins, but they offer better corrosion resistance. If you have a job located near the ocean, galvanized purlins would be a better choice than red oxide purlins.
Here's a comparison of red oxide and galvanized purlins:
Available in Stock
We maintain a comprehensive stock of Z purlin sizes, lengths, and depths, including Z purlins and C sections. We've got a wide range of options to choose from, with standard lengths available up to 6.100m.
Our Z purlins are ideal for use with corrugated panels or box profile sheets. They come in common depths of 177mm and 200mm.
For specific requirements, you can use the following codes when contacting our team: CS17716 for 177mm depth with 1.6mm thickness.
Design and Installation
Design and installation of a C purlin roof involves several key considerations.
The distance between C purlins can range from 1.5 to 2.5 meters, depending on the design requirements and the type of roofing material used.
For a C purlin roof, the purlins should be spaced at a maximum of 1.5 meters to ensure the roof can withstand wind loads and other external factors.
A typical C purlin roof design consists of a series of C-shaped steel beams that span between the roof rafters, providing additional support and stability.
The C purlins are usually installed at a height of around 0.5 to 1 meter above the roof rafters, depending on the specific design requirements.
For your interest: Purlins and Rafters
Structural Aspects
Structural Aspects play a crucial role in the design and installation of roofing systems. Effective load transfer and stability are ensured through the use of C-purlins, characterized by their "C" shape with flanges on each side.
The cross-sectional shape and dimensions of the purlin, known as its sectional properties, determine its load-bearing capacity. This is particularly important when using cold-formed steel sections, such as C or Z profiles, which offer a favorable strength-to-weight ratio.
See what others are reading: Calculating Snow Load on Pitched Roof
Purlins function as load-bearing members, distributing the roof's weight to the supporting structure, which may include columns, beams, or load-bearing walls. Proper engineering and design are essential to ensure loads are allocated efficiently to prevent overloading.
The connection details between the purlins and the main structural elements are critical for ensuring load transfer. Standard connections include welded or bolted connections, which must be designed to account for the specific loads and forces involved in the structure.
The spacing and spans of the purlins are carefully determined during the design phase to meet structural requirements. This influences the distribution of loads and the overall stability of the roofing system.
To illustrate the importance of spacing and spans, consider a typical roof with a span of 20 feet. In this case, the purlins would be spaced at 4 feet on center, with the exact spacing determined by the design engineer based on the load-bearing capacity and structural requirements of the roof.
Here are some key factors to consider when designing the structural aspects of a roofing system:
- Sectional properties: Determine the load-bearing capacity of the purlin based on its cross-sectional shape and dimensions.
- Load distribution to supports: Ensure loads are allocated efficiently to prevent overloading.
- Connection details: Design connections to account for specific loads and forces involved in the structure.
- Spacing and spans: Determine the spacing and spans of the purlins to meet structural requirements.
- Deflection control: Control bending or sagging of purlins under load to maintain the roofing system's integrity.
Spacing
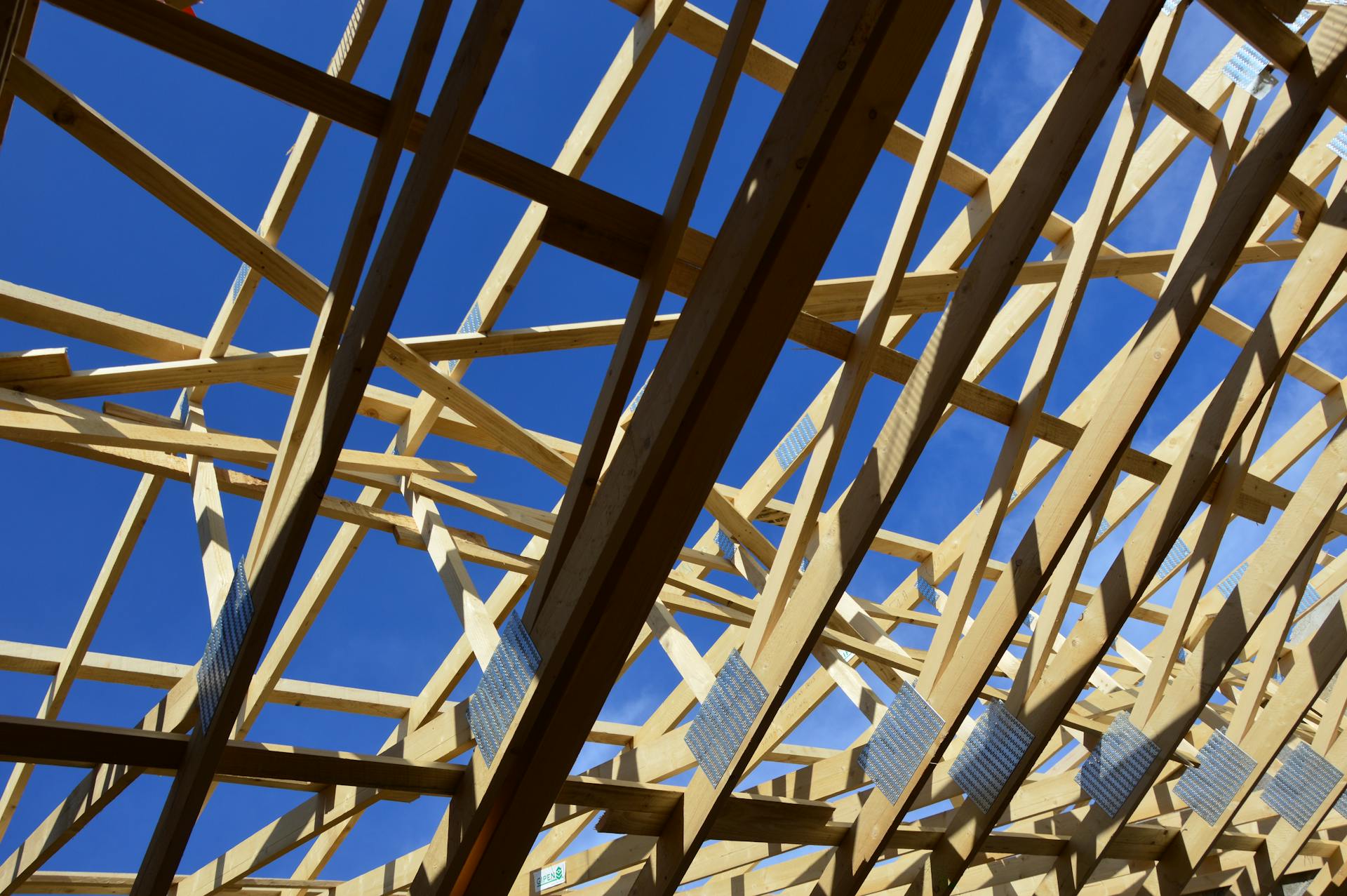
Spacing is a critical aspect of purlin design and installation. The spacing between purlins determines the load distribution to supports, which is essential for preventing overloading.
Purlin spacing is typically determined by the weight that the structure will carry and the load capacity of the metal panels. For heavier loads, shorter distances between purlins are required to provide sufficient support.
The engineer will use metal panel and purlin load charts to determine the correct purlin spacing for your project. This chart will help you find the optimal balance between purlin spacing and material cost.
A shorter purlin spacing will result in a higher material cost, but it will also ensure the structural integrity and stability of the construction project. On the other hand, a longer purlin spacing may save on material cost, but it may compromise the structural integrity of the project.
Here's a general guideline for purlin spacing:
Keep in mind that this is a general guideline and the actual purlin spacing will depend on the specific project requirements and the load capacity of the metal panels. It's always best to consult with a professional engineer to determine the correct purlin spacing for your project.
For more insights, see: Purlins Spacing
Frequently Asked Questions
Is C purlins good for roofing?
Yes, C purlins are suitable for roofing as they can support the weight of roofing materials and beams. They play a crucial role in building a sturdy roof structure.
What is stronger, C purlin or Z purlin?
Z purlins are stronger than C purlins, making them a better choice for buildings with heavy loads or large roofing areas.
Sources
- https://www.kloecknermetals.com/blog/the-ultimate-guide-to-purlins-in-metal-roofing-steel-frame-construction/
- https://www.westernstatesmetalroofing.com/blog/metal-purlins
- https://etas-inc.com/metal-roofing-purlins/
- https://www.maxroof.in/diference-between-c-and-z-purlin.html
- https://cardinalsteels.com/z-purlins-and-sections/
Featured Images: pexels.com