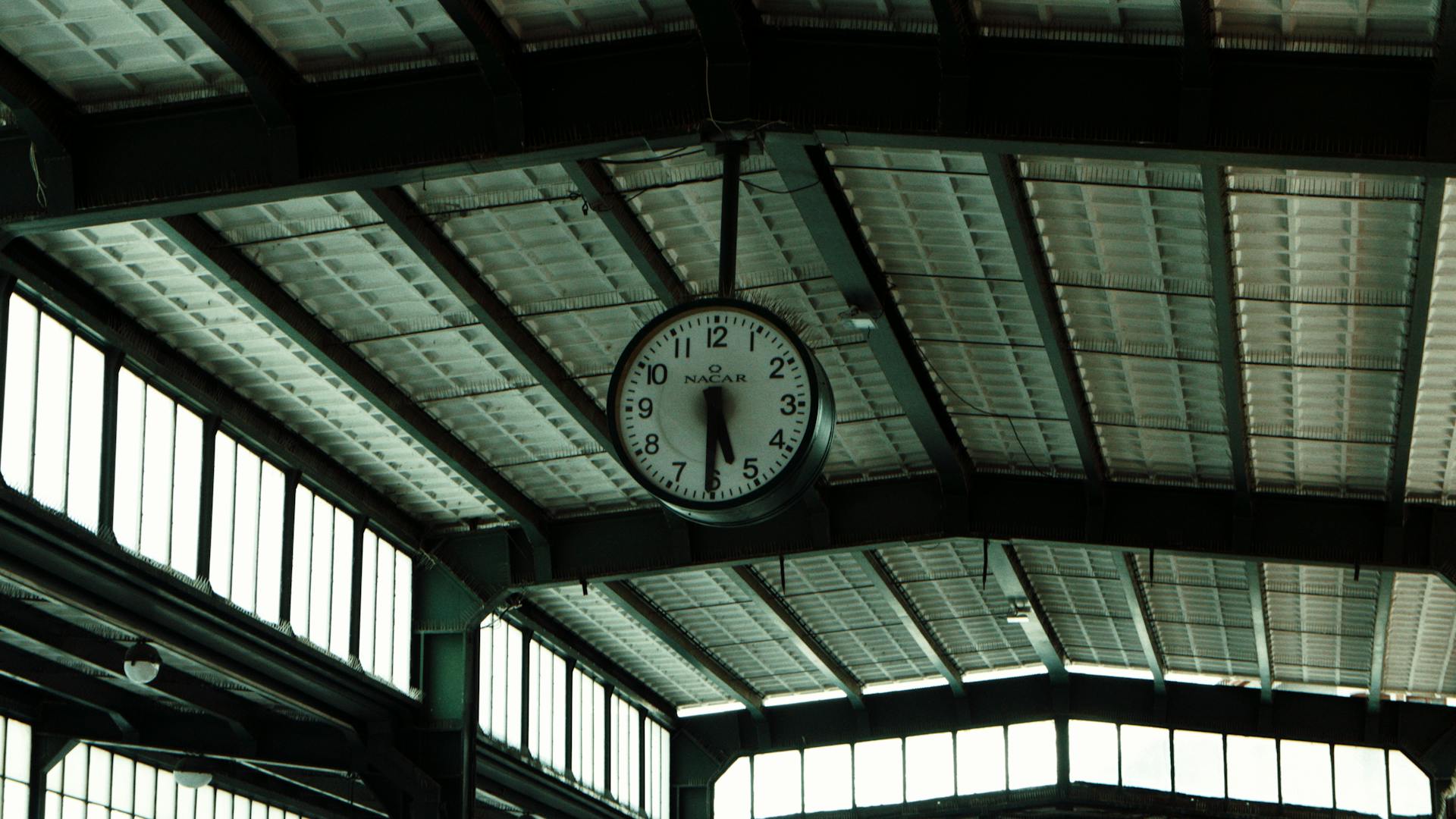
Optimizing purlins spacing is crucial for a sturdy and efficient roof system. Typically, purlins are spaced between 24 and 40 inches on center.
The American Society of Civil Engineers recommends a minimum spacing of 24 inches for most roof types. This allows for adequate support and distribution of loads.
A common spacing of 32 inches on center is often used for residential roofs. This balance between cost and structural integrity is a good starting point for many builders.
The International Building Code specifies that purlins must be spaced no more than 40 inches on center for certain types of roofs, such as those with high winds or heavy snow loads.
You might like: Types of Purlins
What Is a Purlin?
A purlin is a horizontal beam used in building construction to support and stabilize a metal roofing or wall structure. It's typically made of metal, such as steel, aluminum, or hot-dipped galvanized steel.
Purlins come in various shapes, including C purlins and Z purlins. They're designed to distribute the load of the roof or wall to the main structural elements.
See what others are reading: How to Install Purlins for a Metal Roof
In commercial and industrial buildings, and some residential metal roofs, metal purlins are commonly used to provide structural support. They're lightweight yet sturdy, making them cost-effective and easy to handle during installation.
Metal purlins are durable and provide excellent structural support, allowing for greater design flexibility and the ability to span long distances without the need for supporting columns or beams.
For another approach, see: Steel Building Purlins
Types of Purlins
Metal purlins play a crucial role in the secondary frame of a metal building. Choosing the right type is essential for a sturdy and long-lasting structure.
There are several types of metal purlins to consider, and each has its own unique characteristics. Contacting experts like Titan Steel Structures can help determine which type is best for your project.
A key consideration is the type of metal used for the purlin, with different materials offering varying levels of strength and durability.
See what others are reading: Metal Roof Purlins or Sheathing
Purlins Technical Details
Purlins are a crucial part of any building's structure, providing support and stability to the roof. Purlins are typically made of wood or metal and are spaced at regular intervals to ensure even weight distribution.
In terms of technical details, purlins can be constructed with a variety of materials, including wood and metal. The choice of material often depends on the specific needs of the building project.
A common technical detail for purlin construction is the use of a 45-degree angle to secure the purlin to the side rail, ensuring a strong and stable connection.
Technical Details
Purlins are typically made from wood or steel, with wood being a popular choice due to its sustainability and cost-effectiveness.
The size of purlins can vary, but they are often around 150-200mm deep and 50-100mm wide, with a thickness of 10-20mm.
The spacing of purlins depends on the design and load requirements of the building, but they are usually spaced between 600-1200mm apart.
Side rails are usually made from the same materials as purlins and are designed to support the roof's weight, with a typical depth of 150-200mm and width of 50-100mm.
Recommended read: Wood Purlins
Eaves beams are often larger than purlins, with a depth of 250-300mm and a width of 100-150mm, and are used to support the roof's edge.
Mezzanine floor joists are typically made from wood or steel and are designed to support the weight of the mezzanine floor, with a depth of 150-200mm and a width of 50-100mm.
Consider reading: How to Support Roof Purlins
Z Section Steel
Z Section Steel is a type of purlin that's widely used in construction. It's named for its resemblance to the letter Z, and it's known for its exceptional strength and durability.
These purlins offer overlapping joints, making them stronger than C purlins. This feature also allows for more efficient use of materials, as it reduces the required purlin height.
Z Section Steel purlins are commonly used in agricultural and industrial buildings due to their versatility and lightweight properties. They can be used in a variety of building sizes and can be paired with other accessories like sleeves and cleats.
Z Section Steel purlins are made from cold rolled steel and come in a range of depths, from 142mm to 342mm deep. They're also pre-hot dipped galvanized for added durability.
Here are some key features of Z Section Steel purlins:
- Superior strength
- Purlins can be overlapped
- Save material by reducing purlin height
Z Section Steel purlins have a minimum yield strength of 450N/mm², making them a reliable choice for large-scale structures.
Purlin Materials and Finishes
Purlin materials can be made from steel, aluminum, or wood, with steel being the most common choice due to its strength and durability.
Steel purlins are often coated with a galvanized layer to protect against corrosion, but other finishes like polyester powder coating and silicone-modified polyester are also used.
The thickness of purlin materials varies depending on the load-bearing requirements and the type of purlin, but a typical thickness for steel purlins is between 1.5 and 3 millimeters.
Steel Finishes
Steel finishes are available in two types, and understanding the differences can help you choose the right one for your project.
Steep purlins are available in two finishes, which can be a game-changer for your construction project.
The two types of steel finishes are critical to consider when selecting the right purlin for your needs.
Understanding the differences between the finishes can help you make an informed decision and avoid costly mistakes down the line.
Steel Finishes: Understanding the Differences
Galvanized steel is coated with a layer of zinc to protect it from corrosion, making it a popular choice for purlins.
Hot-dip galvanizing involves dipping the steel in a bath of molten zinc, creating a strong bond between the zinc and the steel.
The galvanized coating can be further enhanced with a clear organic coating to provide additional protection.
Pre-galvanized steel, on the other hand, is coated with zinc before being formed into a specific shape.
Galvanized steel is more resistant to corrosion than pre-galvanized steel due to the additional layer of zinc.
A powder coat finish is a popular choice for steel purlins, offering a durable and chip-resistant surface.
Powder coating involves applying a powdered paint to the steel using an electrostatic charge.
This process creates a strong bond between the paint and the steel, resulting in a long-lasting finish.
The powder coat finish can be applied in a range of colors and is often used to match the color of the roofing material.
Purlin Sizes and Gauges
Purlin sizes can range from 4” to 12” with a flange width of 1-½” to 4”, and are available in custom sizes and lengths.
Purlins are offered in three common gauges: 12 gauge, 14 gauge, and 16 gauge.
The choice of gauge depends on the specific requirements and demands of the construction project, with each gauge having its unique strength and load-bearing capabilities.
Readers also liked: Zed Purlins Sizes
Sizes
Purlin sizes can vary, but they're typically between 4” and 12” wide.
The flange width of purlins can be anywhere from 1-½” to 4”.
Purlins are available in custom sizes and lengths to suit specific project needs.
Metal purlins come in three gauges: 12 gauge, 14 gauge, and 16 gauge.
Gauges
When selecting a purlin gauge, it's essential to consider the specific requirements of your construction project.
Metal purlins come in a range of gauges, including 12 gauge, 14 gauge, and 16 gauge.
The choice of gauge depends on the project's needs and demands.
Each gauge has its unique strength and load-bearing capabilities, making it crucial to select the most suitable gauge for optimal structural support.
At ETAS, our team of experts collaborates closely with clients to assess the project's needs and recommend the best purlin gauge accordingly.
With our expertise and knowledge, we ensure that the selected gauge aligns perfectly with the project's specifications, providing the necessary strength and reliability.
Advantages and Return
The advantages of purlins are numerous, and understanding these benefits can help you make informed decisions about purlin spacing.
One of the key advantages of purlins is their superior strength, which allows them to provide excellent support for roofing materials.
Purlins can also be overlapped, which is a big plus when it comes to installation and maintenance.
This overlap feature allows for more flexibility in purlin placement, making it easier to achieve a secure and even roof structure.
By reducing purlin height, you can save material and reduce waste, which is a win-win for your project's budget and the environment.
Here are some key advantages of purlins at a glance:
- Superior strength
- Purlins can be overlapped
- Save material by reducing purlin height
Advantages of Z
Z Purlins offer a range of advantages that make them an excellent choice for building projects. Their unique shape allows for convenient overlapping during installation, which enhances their load-bearing capacity and contributes to more efficient use of materials.
Z Purlins provide superior strength and durability compared to C Purlins, making them a popular choice for large-scale structures. Their ability to withstand heavy loads and harsh weather conditions is unmatched.
One significant advantage of Z Purlins is their ability to save material by reducing purlin height. This is made possible by their overlapping joints, which reduce the required purlin height and make them more efficient.
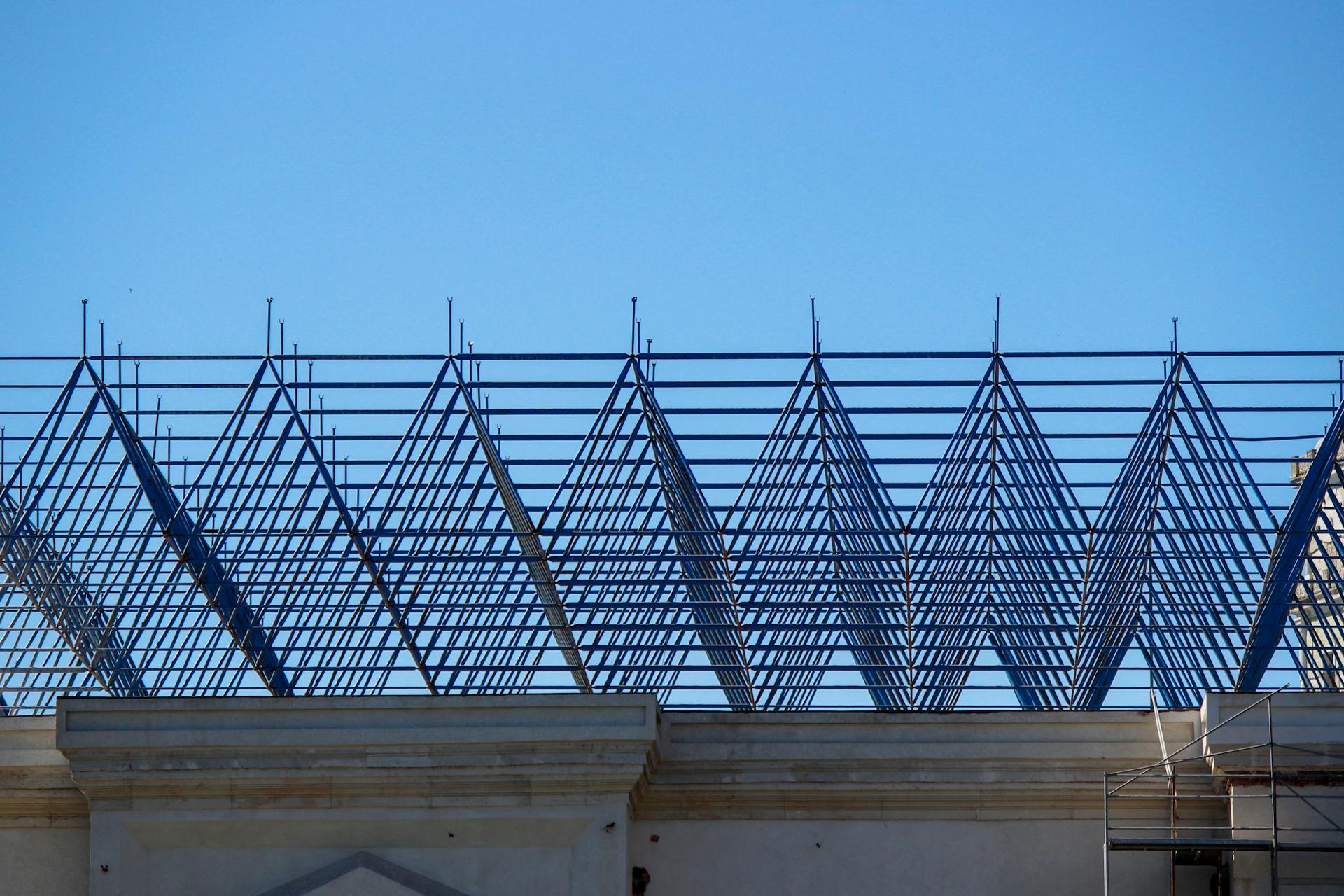
Z Purlins are designed to form the roof and wall joists of a building shell structure, providing a sturdy and reliable support for the roofing sheets. They are also known as zed purlins.
Z Purlins have different sizes and thicknesses depending on the span length and loads of the structure, making them versatile and adaptable for use in various building projects. They can be used with other accessories such as sleeves, cleats, eaves beams, side rails, etc.
Here are some key advantages of Z Purlins:
- Superior strength
- Purlins can be overlapped
- Save material by reducing purlin height
Z Purlins are made from pre-hot dipped galvanised steel, Z275 coating and have a minimum yield strength of 450N/mm², providing lasting performance and structural integrity.
Return
The return on investment for a metal roofing project can be substantial. The cost of materials can be a significant factor in determining the overall cost of the project.
Metal panel and purlin load charts are used to determine the correct purlin spacing for each job, which in turn affects the material cost. This means that the more purlins needed, the higher the material cost will be.
A well-designed metal roofing system can last for decades with minimal maintenance, providing a long-term return on investment.
Frequently Asked Questions
How far can 2x4 purlins span?
For 2x4 purlins, the maximum span is 4 feet. Span limitations may vary depending on specific rafter sizes and configurations.
What is the maximum span of purlins?
The maximum span of purlins varies by size, with eight-inch purlins spanning up to 25 feet. Larger purlins can support longer spans, so check the specific size for your project's needs.
What is the spacing for 2x4 purlins for metal roofing?
For 2x4 purlins under metal roofing, FABRAL recommends spacing them a maximum of 24" on-center. However, in re-roofing jobs with questionable decking, new purlins should be fastened through the decking and into the rafters.
How far apart should purlins be for 26 gauge metal roofing?
For 26-gauge metal roofing, purlins can be spaced up to 4 1/2 feet apart. However, it's recommended to check with a licensed roofing contractor for specific installation requirements.
How far can 2x6 purlins span?
2x6 purlins can span up to 6 feet. However, the actual span may be limited by the size of the supported rafter
Sources
- https://www.hansenpolebuildings.com/2017/05/can-2x4-roof-purlins-span-12-feet/
- https://www.westernstatesmetalroofing.com/blog/metal-purlins
- https://etas-inc.com/metal-roofing-purlins/
- https://www.metsec.com/products/purlins-side-rails/purlins/
- https://titansteelstructures.com/facts/what-are-metal-building-purlins/
Featured Images: pexels.com