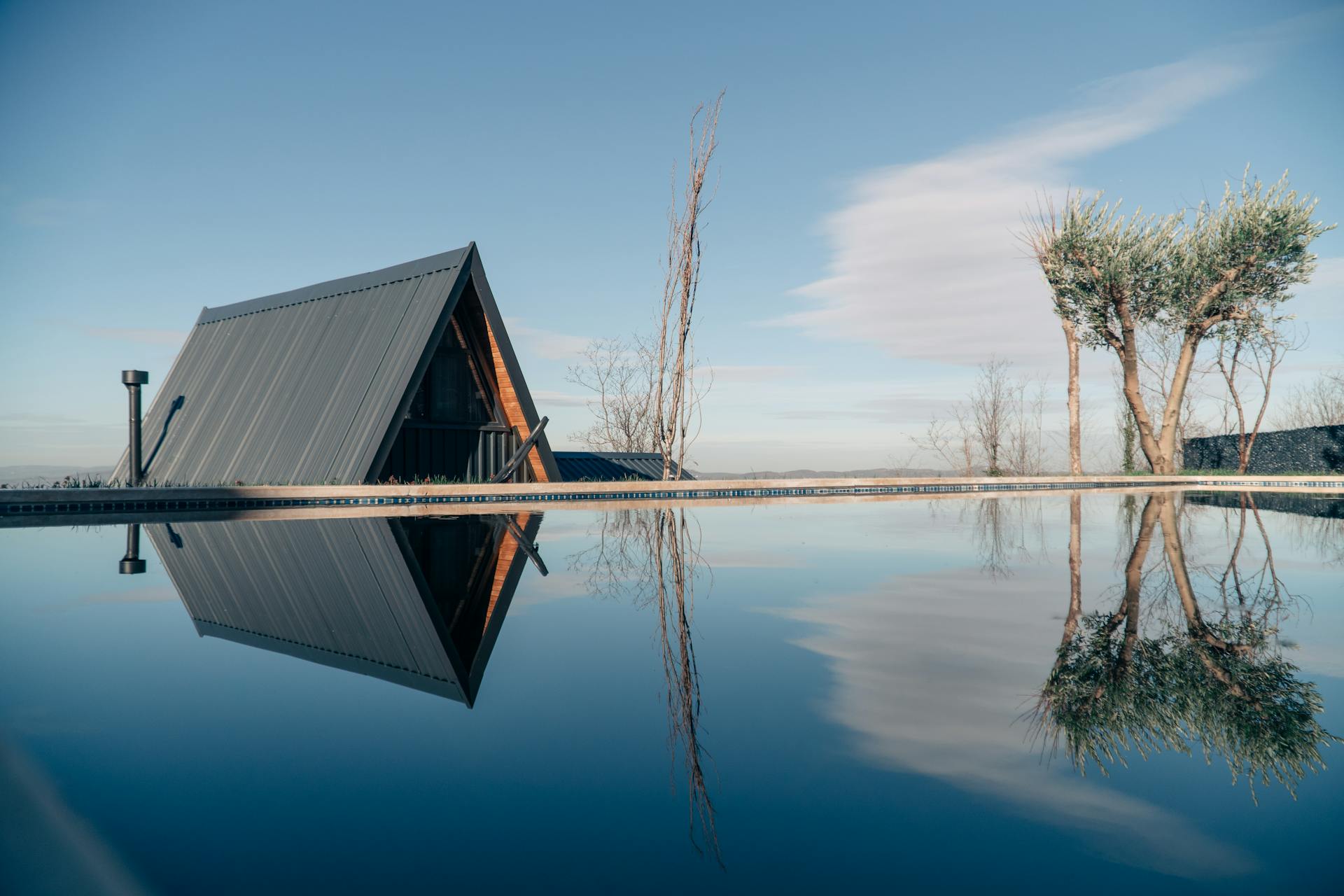
Metal roof purlins are a crucial component of a metal roof system, providing structural support to the roofing materials. They are typically made of steel or aluminum, with a minimum thickness of 0.032 inches.
Purlins are spaced at a maximum of 24 inches on center, depending on the load requirements of the roof. This spacing can vary depending on the type and weight of the roofing material.
A well-designed purlin system can span up to 24 feet without intermediate support, reducing the need for additional framing members.
You might like: Truss System Roof
Types of Metal Roof Purlins
Metal roof purlins come in two main types: C-purlins and Z-purlins. These types are widely used in various construction scenarios.
C-purlins are the most prevalent metal type and are ideal for applications beyond just roofing. They provide structural support for beams used for flooring and walls.
C-purlins have several benefits, including the ability to span length, assured straightness, durability, no side drilling required, and no cutting required.
Here are the key features of C-purlins:
- Ability to span length
- Assured straightness
- Durable
- No side drilling required
- No cutting required
Z-purlins are stronger than C-purlins and are often used in heavy-duty applications.
What Are the Types?
There are two main types of metal purlins: C-purlins and Z-purlins. C-purlins are the most prevalent metal type and find application across various construction scenarios.
C-purlins are characterized by their C shapes or U shapes, giving them structural support for beams used for flooring and walls. They offer several benefits, including the ability to span length, assured straightness, durability, and no side drilling or cutting required.
Z-purlins, on the other hand, are stronger than C-purlins and are often used in heavy-duty applications. They are a key component to the secondary frame of commercial, residential, and industrial metal buildings.
Here are the main types of metal purlins:
Z Purlins
Z Purlins are a type of metal purlin that derives its name from the shape of the letter Z. They are horizontal beams that form the roof and wall joists of a building shell structure.
The shape of Z purlins allows for overlapping joints, making them stronger and sturdier than C purlins. This is a significant advantage in large-scale structures.
A fresh viewpoint: Roof Form
Z purlins are often used because of their superior strength, which is due to the overlapping joints. This unique feature also helps save material by reducing the height of the purlins.
Here are the key advantages of Z purlins at a glance:
- Superior strength
- Purlins can be overlapped
- Save material by reducing purlin height
Purlin Spacing and Size
Metal roof purlins are a crucial component of a building's structure, and their spacing and size play a significant role in determining the overall stability and durability of the roof.
The general rule for spacing metal purlins is that the larger and heavier a metal roofing structure is, the more space is needed between the purlins and the principal rafters. This can range from 12″ up to 24″, but some buildings may require customized spacing depending on the customer's needs.
In general, building codes and manufacturers recommend that purlins should not be more than 30 inches on center when they are used to support steel framing and secondary framing, and 38 inches when only carrying sheathing.
Worth a look: Shed Roof Framing Plan Details
If you're planning a long-span roof, it's essential to use good judgment and consider the following tips:
- If the number of purlins in a span exceeds 5, the center-to-center spacing should not be more than 30 inches.
- For roof spans over 50 feet, consider using purlins in pairs, with a single higher purlin at the center supporting two lower spans at 30 inches apart.
- Place one end post for every long span, at least 200 feet apart, with a bearing plate to support the purlins.
Spacing
Spacing is a crucial aspect of purlin installation, and it's essential to get it right to ensure a sturdy and long-lasting structure. The general rule is that the larger and heavier a metal roofing structure is, the more space is needed between the purlins and the principal rafters.
In most buildings, the common standard distance between purlins and principal rafters ranges from 12″ up to 24″. However, some buildings may require customized spacing depending on the customer's needs.
Many building codes and manufacturers recommend that purlins should not be more than 30 inches on center when supporting steel framing and secondary framing, and 38 inches when only carrying sheathing.
For long spans during light-frame constructions, contractors and engineers should use good judgment when spacing metal roof purlins. Here are some tips to consider:
- If the number of purlins in a span exceeds 5, the center-to-center spacing should not be more than 30 inches.
- For roof spans over 50 feet, consider using purlins in pairs, with a single higher purlin at the center supporting two lower spans 30 inches apart.
- One end post should be placed for every long span, with a bearing plate at least 200 feet long to support the purlins.
The spacing of purlins also depends on the weight that the structure will carry and the load that the metal panels can handle. The heavier the expected load, the shorter the distance between purlins.
A good rule of thumb is to determine the maximum spacing based on the design of the truss, with a maximum spacing of 24″ on center. For wider spans, be sure to factor in the effects of truss bracing, purlin strength, diaphragm strength, and chord forces.
To determine the correct purlin spacing for your project, consult metal panel and purlin load charts. The engineer will use these charts to determine the quantity of metal purlins needed, which in turn will affect the material cost.
For more insights, see: Purlins Spacing
Size of Purlins
Purlins can be manufactured in varying sizes, also known as gauges, with options including 12 gauge, 14 gauge, and 16 gauge.
The most common sizes for purlins are typically between 4” and 12” in width, with a flange width ranging from 1-½” to 4”.
If this caught your attention, see: Zed Purlins Sizes
Single Span
Single Span is a purlin system where the purlin web is bolted to a cleat, unaffected by inward capacities due to bridging.
In this type of span, the outward capacities vary depending on the available number of rows used for bridging.
Here's an interesting read: Life Span of Metal Roof
Purlin Materials and Coatings
Purlin materials and coatings play a crucial role in the durability and longevity of your metal roof purlins. Red oxide and galvanized metal purlins are the two most common types of metal purlins available in the market.
Red oxide purlins have a spray-painted primer with a red finish, which can disguise rust on the structure. However, they only offer minor protection against the elements and will rust quickly without a finished coat of paint. Galvanized metal purlins, on the other hand, undergo a strict zinc-alloy plating process, making them corrosion-resistant and able to resist damage from harsh environments.
Galvanized steel purlins are more suitable for use in corrosive environments, such as near the ocean, and can withstand harsh weather conditions. They are also more difficult to paint compared to red oxide primers.
Red Oxide vs Galvanized
Red oxide and galvanized purlins are two popular options for metal roofing. Red oxide purlins have a spray-painted primer with a red finish, which can disguise rust on the structure. They're also cheaper than galvanized purlins, saving you 25% to 35% on costs.
Galvanized purlins, on the other hand, undergo a strict zinc-alloy plating process, making them resistant to corrosion. They're ideal for harsh environments, such as chemical plants or areas near salt water. However, they can develop white rust when exposed to moisture.
Red oxide purlins are prone to rusting, especially in humid conditions, but the red paint can disguise the rust. Galvanized purlins are more difficult to paint, but they offer better protection against corrosion.
Here's a comparison of red oxide and galvanized purlins:
Choosing Steel and Stud
Steel and Stud is a top choice for purlins due to their expertise in the field, gained from years of production experience.
They offer quality purlins made from quality steel, which is a significant factor in ensuring durability and longevity.
Using advanced technology, Steel and Stud can provide precise measurements, which is crucial for a successful installation.
Their purlins are cut with accuracy, ensuring a smooth and efficient installation process.
Steel and Stud offers consultation services throughout the project, providing valuable guidance and support.
Their consultation services are available until the project is complete, giving you peace of mind and confidence in your decision.
Steel and Stud also offers various designs for metal buildings, allowing you to choose the most cost-effective and safe roofing style for your needs.
These designs are a great way to explore different options and find the perfect fit for your project.
Choosing Materials
The type of purlins you choose will depend on your roof's structural design and pitch. This will dictate the required purlin size and orientation to support the roof effectively.
Different designs require varying purlin sizes and orientations. This is crucial to ensure the roof's stability and longevity.
Finding the right balance between strength and cost savings is key. Larger web sizes provide strength, but may be heavier and more expensive.
In environments prone to corrosion, galvanized purlins are a good option. They offer enhanced durability and resistance to rust, making them a worthwhile investment.
It's essential to balance quality and cost when selecting purlins. Opting for the most economical option that meets the structural requirements can significantly reduce overall project costs.
Here's an interesting read: Metal Roofing vs Shingle Cost
Purlin Designs and Configurations
Purlin sections assume the roof slope, so their spacing must be carefully calculated to follow the nodal pattern for truss support.
There are two types of purlins: Z shapes and C purlins, which can be arranged in various ways depending on the supply length of the sections, the loading and roof span, and the need to avoid wasteful cuts.
The dimensions of these purlins are typically 2 feet by 4 feet, and their installation is similar to that of metal roofs.
Double purlin spans support each other in equal spaces, one on each side and another at the center, which can contain one long and full-length purlin or two purlins lapped together at the central support points.
Take a look at this: How to Support Roof Purlins
Double Span
A double span is a common configuration in purlin designs. It's used to support the weight of the roof decking.
In a double purlin span, two purlins are placed side by side, one on each side of the building. This setup provides additional support and stability.
Double purlin spans support each other in equal spaces, one on each side and another at the center. This helps to distribute the weight evenly.
The double span may contain only one long and full-length purlin or two purlins that are lapped together at the central support points.
Continuous Span
Continuous spans can be achieved with purlins supported at every endpoint of a series of immediate supports that are equally spaced.
The length of the lap for metal purlins is 15% over each support.
For outward loads on the continuous spans, bridging is required at the end.
One less row of bridging may be used for internal spans.
Continuous purlin spans can be made structurally efficient with careful planning.
Purlins are typically installed in dimensions of 2 feet by 4 feet, making them easy to work with.
Their installation is similar to that of metal roofs, which can be beneficial for builders with experience in metal roofing.
Laps
Laps are a crucial aspect of purlin design, and it's essential to understand the best practices for creating them.
Overlapping ends are stronger and preferred compared to butting, so it's best to overlap longer spans for maximum and multiple supports.
Overlap ends at 12″ to ensure a secure connection.
You might like: What Type of Roof Is Best
Purlin laps are recommended at a length of 15% of the span, which provides the necessary structural continuity.
If there are unequal lengths of the span, especially created by reduced end spans, each purlin should have 7.5% of the adjacent span instead of 7.5% of the whole purlin's span.
Purlin laps that are less than 10% of the span may not effectively provide structural continuity and may suffer from failures.
What Are Girts?
Girts are a crucial component in a structural steel construction. They are primarily used in the walls of a building. Steel and Stud uses girts in their constructions, which are made of high-strength steel. Girts are cold formed members extruded to maximize weight and capacity. They are designed to work together with purlins in a building's roof. Steel and Stud offers girts as part of their complete solution for construction, reducing costs for their clients.
Consider reading: Purlins and Girts
Cleats
Cleats play a crucial role in purlin designs and configurations. They come in two main types: single cleats and double cleats.
Single cleats are commonly used in situations where purlins are lapped onto each other, forming a Z shape.
Double cleats are used in instances where successive metal purlins are butted together, which can also help reduce bolt stress in high reaction load areas.
Frequently Asked Questions
Are purlins necessary for a metal roof?
Yes, purlins are a crucial component of metal roofing systems, responsible for distributing the roof's load to the primary structural elements. Without purlins, the roof's integrity and stability would be compromised.
What are the disadvantages of purlins?
Purlins can cause a wavy roof system that stretches metal, leading to screws or nails pulling out. This can compromise the structural integrity and durability of the roof.
What is the spacing for 2x4 purlins for metal roofing?
For metal roofing, FABRAL recommends spacing 2x4 purlins a maximum of 24" on-center. In re-roofing jobs, new purlins should be fastened through the decking and into the rafters for added stability.
Which is stronger, C or Z purlins?
Z purlins are stronger than C purlins, making them ideal for buildings with heavy loads or large roofing areas.
How far can metal purlins span?
Metal purlins can span up to 30 feet with a 10-inch diameter, and smaller diameters can span shorter distances. Check the specific span for your purlin size in the table below.
Sources
- https://www.steelandstud.com/purlins/
- https://blog.mcelroymetal.com/metal-roofing-contractors/the-ultimate-guide-to-metal-roof-purlins-importance-and-installation-tips
- https://www.vcalc.com/wiki/purlins-for-a-gable-roof
- https://www.kloecknermetals.com/blog/the-ultimate-guide-to-purlins-in-metal-roofing-steel-frame-construction/
- https://www.westernstatesmetalroofing.com/blog/metal-purlins
Featured Images: pexels.com