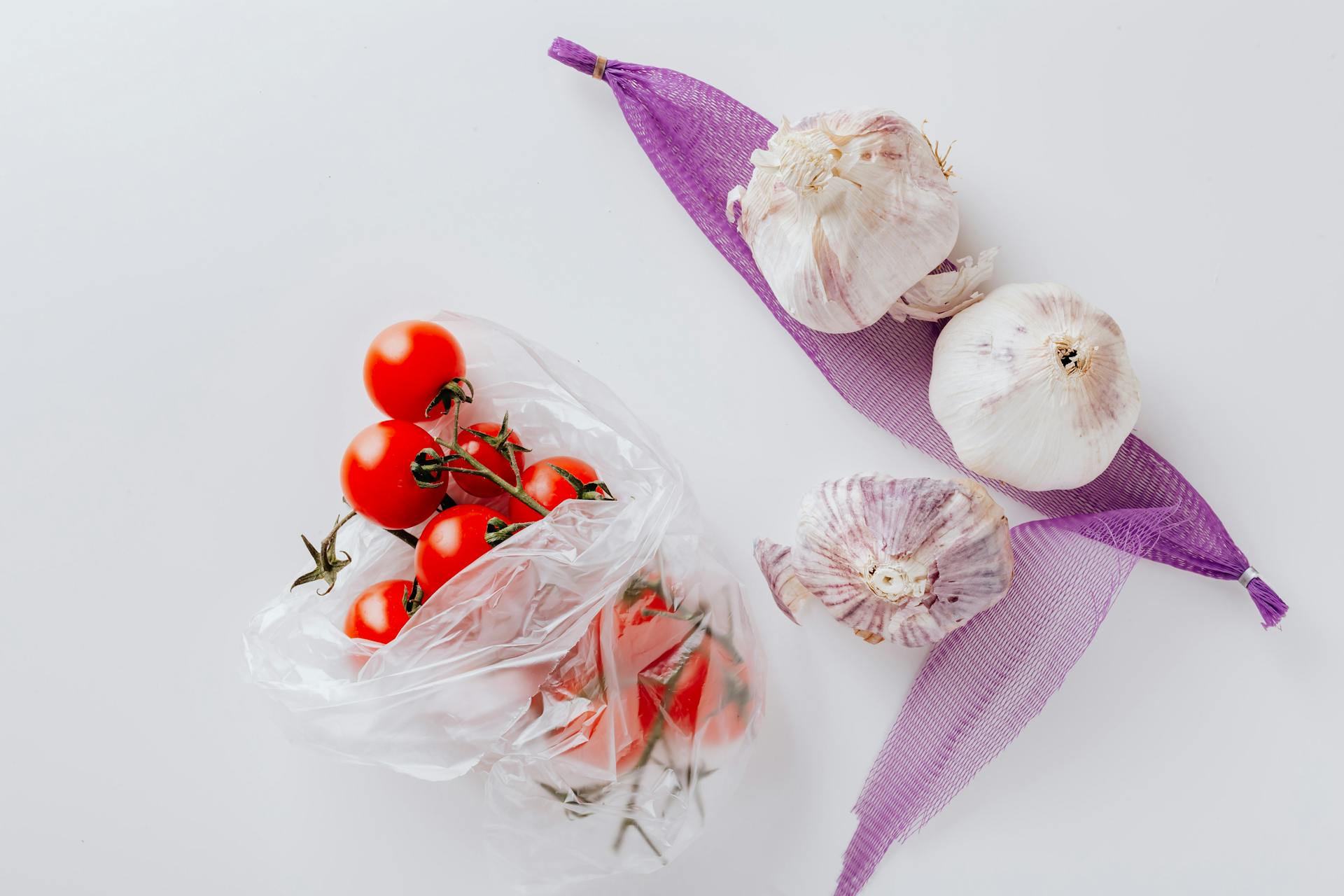
Polyethylene pipes are a popular choice for water supply due to their durability and resistance to corrosion. They can withstand high pressures and temperatures, making them ideal for transporting water over long distances.
Polyethylene pipes are also resistant to scaling and biofouling, which can clog traditional metal pipes and reduce water flow. This means less maintenance and upkeep for homeowners and municipalities alike.
In fact, polyethylene pipes can last for up to 50 years or more, depending on the quality of the pipe and installation. This is significantly longer than traditional metal pipes, which can corrode and fail within 20-30 years.
Their flexibility also makes them easier to install and transport, reducing labor costs and minimizing the risk of damage during installation.
Polyethylene Pipe Installation
Polyethylene pipe installation requires careful planning to ensure a successful and efficient setup process. First, you need to prepare a trench where the pipes will be laid, which entails digging a trench deep enough for the pipe diameter but ensuring sufficient cover to protect from the outside.
To achieve a seamless joint, HDPE pipes can be welded together using either electrofusion or butt fusion techniques. This reduces the chances of leaks and creates a strong connection.
A common mistake to avoid is neglecting proper soil preparation, as poorly compacted or rocky soils may cause pipe misalignment or damage over time. You should also follow manufacturer guidelines for joining and handling pipes to ensure weak connections don't occur.
Here are some essential tools and equipment needed for installation:
- Trenching Equipment: Trenchers or shovels for digging trenches
- Pipe Cutting Tools: Saws or other suitable tools for cutting polyethylene pipe lengths
- Joining Tools: Clamps and fusion welding equipment for joining pipes
- Pressure Testing Equipment: Pressure gauges and fittings for leak tests
- Measuring Tools: Measuring tape and level for precise alignment and locations of pipes
- Safety Gear: Personal protective clothing such as gloves, glasses, and steel-toe shoes
Step-by-Step Installation Guide
To install polyethylene pipes for water systems, you need to plan your installation carefully. This involves reading through local codes and regulations regarding polyethylene pipe installation to ensure compliance and safety procedures are correctly followed.
First, you need to prepare the trench where the pipes will be laid. Dig a trench that is at least 12 inches more than the width of the tube on either side and deep enough to keep them below frost lines, which are common in most places, like 36 inches. This will protect pipes against freezing.
Broaden your view: When Will Water Pipes Freeze
Next, install the HDPE pipes into the trench, ensuring they align well and pay attention to bends and joints to prevent disrupting smooth flow.
To join the pipes, you can use either electrofusion or butt fusion techniques, following welding instructions from manufacturers to achieve strong seams without leaks.
Backfill the soil into the trench gently, without damaging the tubes, and compress the soil lightly to eliminate air pockets.
Finally, perform a leak check by pressurizing the pipes before commissioning the system. Document all specifications of materials used and where they were located for future maintenance or modifications.
Here's a summary of the tools and equipment needed for installation:
Installation Mistakes to Avoid
Neglecting proper soil preparation is a common mistake that can lead to pipe misalignment or damage over time.
If you don't compact the soil properly, it can cause the pipes to shift or crack. I've seen this happen before, and it's not a pretty sight.
Overlooking manufacturer guidelines can result in weak connections. Always make sure to follow the manufacturer's instructions for joining and handling pipes.
Insufficient leak testing can cause severe problems in the future. Don't skip the pressure test – it's an essential step in ensuring your installation is successful.
Here are some common installation mistakes to watch out for:
- Neglecting proper soil preparation
- Overlooking manufacturer guidelines
- Insufficient leak testing
Transportation Network Rebuild
Rebuilding a water transportation network with polyethylene can be a game-changer for cities with aging infrastructure.
The city of Palermo, Italy is a great example, where the population grew from 300,000 to over 700,000 after World War II, putting a huge strain on the aging cast iron water network.
Water leakage rates exceeded 40% in some parts of the network, making it a pressing issue that needed to be addressed.
The city planners and an Italian water company designed a new water network that could deliver 430 liters per inhabitant per day for a projected population of a million citizens.
A unique perspective: City Water Pipes inside
This system was designed to last through to 2040, requiring a solution that was both durable and efficient.
HDPE pipe was chosen for its lightweight and flexibility, enabling fast installation and fewer fittings.
The ability to join HDPE pipe with heat fusion provided the highest potential for leak-proof joints within the system.
A one-year follow-up on the installation demonstrated satisfactory results, showcasing the effectiveness of polyethylene pipe installation in rebuilding a water transportation network.
Horizontal Directional Drilling
Horizontal directional drilling is a trenchless installation technique that minimizes surface footprint.
It allows for controlled direction of the drilling to avoid obstacles like interstate highways.
HDPE pipe is a suitable choice for this technique due to its high strength and flexibility.
HDPE pipe can endure minor surface perturbations during installation without damaging its integrity.
This makes it an ideal material for use in horizontal directional drilling projects.
The technique was determined to be the best approach for a project in Carlsbad, California, where a pipeline needed to be installed uphill and below an interstate highway.
HDPE pipe was chosen to complement the installation technique due to its properties.
Polyethylene Pipe Qualities
Polyethylene pipe is a game-changer for water supply systems. Its unique qualities make it an ideal choice for transporting potable water.
HDPE pipes are incredibly durable, with a service life of 50 to 100 years. This means they can withstand harsh environmental conditions and last longer than traditional pipes.
The smooth internal surface of HDPE pipes ensures hydraulic efficiency, minimizing the risk of water loss and contamination. This is particularly important in potable water applications where the safety of the water supply is paramount.
One of the most significant advantages of HDPE pipes is their resistance to corrosion and chemical attack. This means they can handle saltwater, corrosive soils, and aggressive flow streams without compromising the water quality.
HDPE pipes are also flexible, making them easier to install in rugged terrains. This flexibility also helps to minimize the need for fittings, improving the overall hydraulic efficiency of the system.
Here are some key benefits of HDPE pipes:
- Leak-free fused joints
- Chemical resistance
- Durability and flexibility
- Extreme surge tolerance
- Temperature resistance
- Easy installation with trench-less technologies
HDPE pipes can handle a wide range of temperatures, from -40°F to 140°F, making them suitable for use with hot or cold water in various environments. This flexibility is a significant advantage in areas with extreme temperature fluctuations.
Overall, HDPE pipes offer a unique combination of durability, flexibility, and resistance to corrosion and chemical attack, making them an ideal choice for water supply systems.
Polyethylene Pipe Applications
Polyethylene pipes are used in many applications, including water supply lines, irrigation systems, natural gas transportation, sewer systems, and more. They are versatile and reliable for both residential and commercial projects.
PE pipes are perfect for irrigation systems because they are lightweight and easy to handle. Their flexibility allows for easy directional changes without the need for additional fittings.
HDPE pipes are used in a variety of applications, including:
- Offering HDPE Water Supply Systems
- HDPE Pipe for Water Distribution System
- HDPE pipe of potable water supply
- HDPE water purifier, treatment water plants, water supply pipelines
- HDPE and PVC pipelines for the transport of water
- HDPE Irrigation & Water Systems
- Town water system
- Civil construction for water supply
HDPE pipes are also used in the fields of aquaculture.
Benefits
Polyethylene pipes have numerous benefits that make them an ideal choice for water supply systems.
Polyethylene pipes are highly resistant to corrosion and chemicals, ensuring safe and clean drinking water at all times. This is due to their inert properties, which prevent them from reacting with minerals or chemicals in the water.
Their lightweight and flexible nature makes them easy to handle and install, reducing labor costs and transportation costs. Additionally, their coil format allows for more accessible transportation and installation, reducing the number of joints needed and speeding up the installation process.
Polyethylene pipes can withstand harsh environmental conditions, including extreme temperatures, UV radiation, and ground movement, reducing cracks and leaks in the pipes. They also resist biological growth and mineral scaling, ensuring a smooth inner surface and optimal water flow.
Here are some key benefits of polyethylene pipes:
- Lightweight and easy to handle
- Excellent durability and resistance to cracking and leaking
- Corrosion resistance and chemical resistance
- Flexibility and ease of installation
- Leak-free and recyclable
Their long service life, typically up to 50 years, reduces maintenance costs and lifecycle expenses. With minimal maintenance required, polyethylene pipes are a cost-effective and efficient choice for water supply systems.
HDPE pipes, in particular, have a range of advantages, including high strength, durability, and impact resistance, making them suitable for use in different areas. They also have excellent chemical resistance, enabling good service life even when exposed to aggressive fluids.
Overall, polyethylene pipes offer a range of benefits that make them an ideal choice for water supply systems, including their lightweight and flexible nature, corrosion resistance, and long service life.
Regular Maintenance Tips
Check your polyethylene water pipes regularly every few months to catch any potential leaks or cracks before they become real problems.
Regular inspections are recommended to ensure no leaks or damages, but overall, they offer a low-maintenance piping solution.
To identify any signs of wear or damage, including cracks or leakage, perform regular check-ups.
Cleaning the external part of pipes can prevent substances from building up that may destroy the pipes.
An area with a leak must be separated, drained, and repaired using an appropriate method, like mechanical joints or fusion welding.
Ensure this conforms to all local rules on safety when performing such repairs at any given time.
Fusion welding works very well to fix leaks because it forms strong bonds that restore pipe integrity.
Regular monitoring should be done, and timely maintenance should be maintained to keep your polyethylene water pipes in good condition.
By being proactive about maintenance issues and dealing with them promptly, you can vastly enhance the service duration of polyethylene water pipes.
Frequently Asked Questions
What is the disadvantage of polyethylene pipe?
HDPE pipes are prone to stress cracking, flammability, and chemical damage, making them a less-than-ideal choice for certain applications.
Sources
- https://agruamerica.com/pe-pipe-for-water-supply/
- https://sinopipefactory.com/blog/why-choose-polyethylene-pipe-for-your-water-supply-the-ideal-piping-solution/
- https://www.fhs.com.au/fusion-melding-blog/why-choose-polyethylene-pipes-for-water-supply-systems
- https://wlplastics.com/potable-water/
- https://www.bingopipes.com/High-Density-Polyethylene-Drinking-Water-Pipes.html
Featured Images: pexels.com