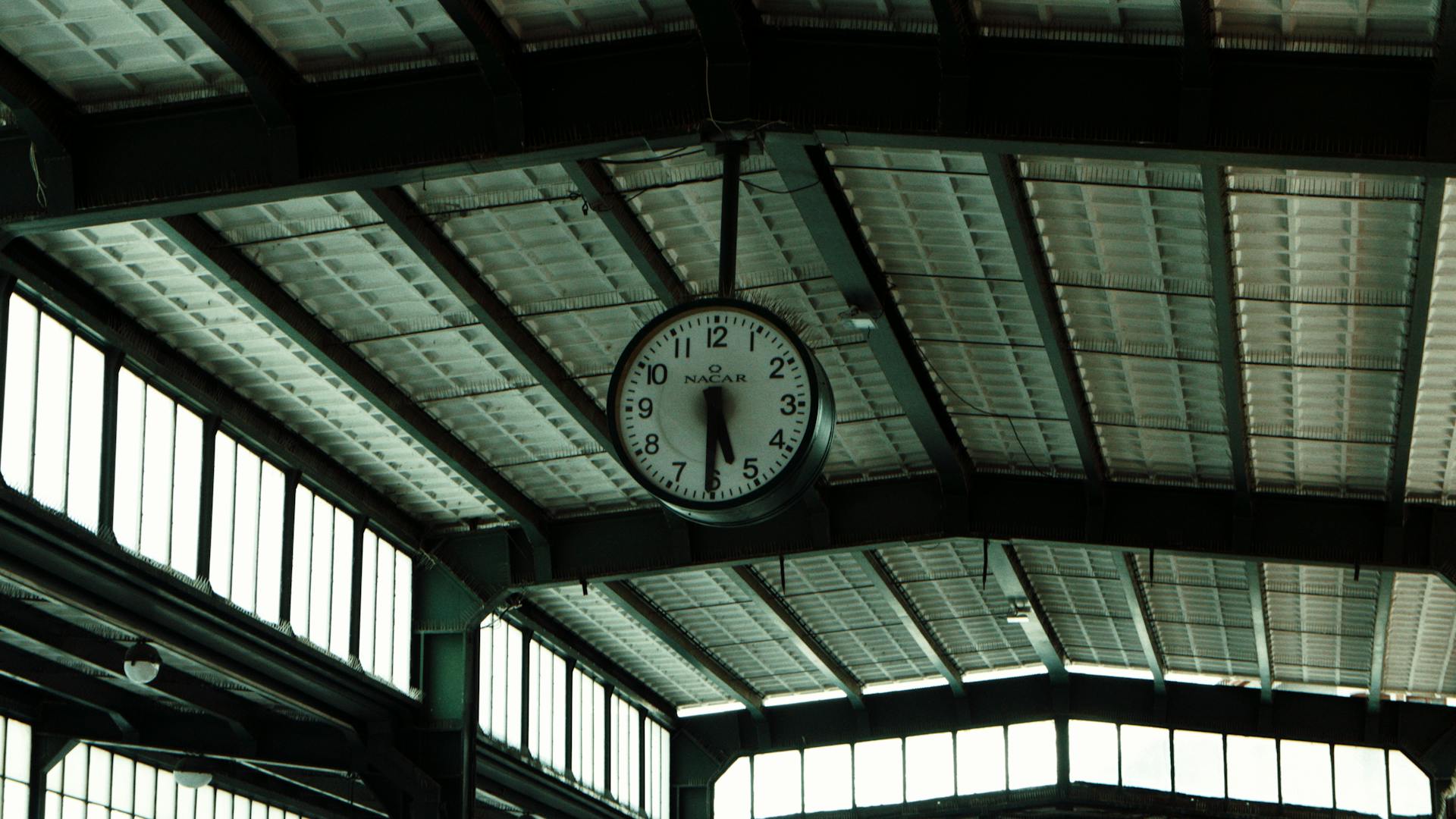
Purlins are horizontal beams that provide essential support to roofs, and understanding their types, materials, and installation is crucial for any construction project.
There are three main types of purlins: solid purlins, lattice purlins, and built-up purlins.
Solid purlins are made of a single piece of material, usually wood or steel, and are commonly used in smaller roofs.
Lattice purlins, on the other hand, are made of a framework of wood or steel, providing more support and stability than solid purlins.
Built-up purlins are constructed by layering multiple materials, such as wood or steel, to create a strong and durable beam.
Purlins can be made from a variety of materials, including wood, steel, aluminum, and fiberglass.
For your interest: Types of Purlins
Types of Purlins
Purlins come in two main types: C-purlins and Z-purlins.
C-purlins are the most prevalent metal type, finding application across various construction scenarios.
Z-purlins are stronger than C-purlins.
They are often used in heavy-duty applications.
Intriguing read: How to Install C Purlins
Purlin Materials
Purlins can be made from a variety of materials, but the most common ones are steel and wood.
Steel purlins are a popular choice because they're lightweight, dimensionally stable, and can withstand extreme temperature changes. They're also relatively inexpensive and easy to work with.
Cold-formed steel is the most common material used to make steel purlins, as it's thin enough to put screws through and is less expensive than hot-rolled steel.
Wood purlins, on the other hand, can be prone to rot if not properly maintained. They're best dried before installation to prevent moisture from accumulating and adding weight, which can cause them to sag.
A protective coating is often applied to steel purlins to prevent corrosion, and a layer of paint is also applied to provide additional protection. This combination of zinc and paint provides corrosion protection that's approximately twice as effective as either one alone.
Wood
Wood purlins can be a great option for use with fiber cement sheeting, ensuring a breathable room that's safe for storing organic materials like livestock or grain.
Wood purlins are made from wood, which can rot over time.
Drying wood purlins before installation is crucial to prevent moisture-related issues.
The main problem with wood purlins is that they can be dry when installed, which can lead to sagging due to added weight from moisture.
Wood purlins can be a good choice for certain applications, but they require special care to ensure they last.
Check this out: Wood Purlins
Steel
Steel purlins are a great alternative to wood purlins, offering a lightweight and dimensionally stable option that expands and contracts reasonably in extreme temperature changes.
Steel purlins are made from cold-formed steel, which is rolled or pressed into the desired shape. This material is less expensive for manufacturers than hot-rolled steel and is also easier to work with.
Cold-formed steel is stronger than hot-formed steel, but it's more likely to break under pressure than bend.
Hot-dipped galvanized steel is often used to manufacture purlins, providing a coating that gives good protection in most exposed internal environments.
To protect purlins from corrosion, a layer of paint is applied outside, creating a synergistic effect that provides corrosion protection approximately 2X the sum of the corrosion protection that each alone would provide.
Steel purlins can be manufactured to have a web height of 4″ min – 20″ max, with a flange size of 1⅝″ min – 4½″ max, and a steel thickness of 0.059″ (16ga) min – 0.128″ (10ga) max.
Chinh Dai Steel, a professional supplier, specializes in producing high-quality purlins that are popular in many international markets, including Australia, India, and Indonesia.
Red Oxide vs Galvanized
Red oxide and galvanized metal purlins are two finishes that protect bare steel from rust. Galvanized metal purlins are coated with a zinc-alloy plating that makes them corrosion-resistant.
Galvanized metal purlins can withstand harsh environments like chemical plants or areas near salt water. However, they're not resistant to oxidizing and can develop an unattractive white rust when exposed to moisture.
Red oxide purlins, on the other hand, develop a surface rust that's disguised by their painted red coloring. This makes them a good option for environments where a red color is desired.
Red oxide purlins are best if you need a finish that can withstand moisture and still maintain a red color.
Worth a look: Red Iron Purlins
Lumber Grade
When working with purlins, it's essential to consider the lumber grade. A higher-grade lumber can make a smaller purlin stronger than a larger one made of lower-grade lumber.
Smaller purlins can actually carry a heavier load if they're made of high-grade lumber. In fact, a 2" x 8" purlin made of higher-grade lumber may be more substantial in bending, compression, and tension values than a larger 2" x 10" piece.
Using smaller sized purlins with higher-grade lumber is a good practice. This is because high-grade lumber can provide better structural integrity.
Here are some key takeaways:
- Use smaller sized purlin with higher-grade lumber
- Avoid using larger sized purlin with lower-grade lumber
Purlin Design and Installation
Purlins are installed horizontally under metal roofs, typically on top of roof rafters with a felt underlayment or vapor barrier installed above. They provide added support to the roof and a nailing surface for the end panels and drip edges.
Purlins are usually 2 by 4 feet in size and are installed similarly to metal roofing. They must be bolted in the top web hole and the lower flange holes at both ends of the lap to provide full structural continuity.
Purlin laps that are bolted only in the web of lapped purlins do not provide full structural continuity and can be prone to pressure from excessive loads.
Here are some key considerations for purlin design and installation:
- Sectional properties: The cross-sectional shape and dimensions of the purlin determine its load-bearing capacity.
- Load distribution to supports: Purlins distribute the roof's weight to the supporting structure, which may include columns, beams, or load-bearing walls.
- Connection details: The connection details between the purlins and the main structural elements are critical for ensuring load transfer.
- Spacing and spans: The spacing and spans of the purlins are carefully determined during the design phase to meet structural requirements.
- Deflection control: Engineers consider deflection limits to control the bending or sagging of purlins under load.
Structural Aspects
Structural Aspects are crucial when it comes to purlin design and installation. The cross-sectional shape and dimensions of a purlin, known as its sectional properties, determine its load-bearing capacity.
Cold-formed steel sections, such as C or Z profiles, are often used due to their favorable strength-to-weight ratio. This is a significant advantage, as it allows for more efficient use of materials.
Proper engineering and design are essential to ensure load transfer between purlins and the main structural elements. The connection details between these components are critical for load transfer.
Welded or bolted connections are standard, and their design must account for the specific loads and forces involved in the structure. Engineers consider factors like load distribution and support to prevent overloading.
The spacing and spans of purlins are carefully determined during the design phase to meet structural requirements. This influences the distribution of loads and the overall stability of the roofing system.
To control deflection, engineers consider deflection limits to prevent excessive bending or sagging of purlins under load. Design calculations aim to maintain the roofing system's integrity within acceptable limits.
Here are some key factors to consider when designing purlin structural aspects:
- Sectional Properties: Determine the load-bearing capacity based on cross-sectional shape and dimensions.
- Load Distribution to Supports: Ensure efficient load transfer to the supporting structure.
- Connection Details: Design connections to account for specific loads and forces.
- Spacing and Spans: Determine spacing and spans to meet structural requirements.
- Deflection Control: Consider deflection limits to maintain the roofing system's integrity.
Predrilled
Predrilled purlins are a game-changer in construction. They ensure that the material is not damaged by nail guns during the assembly process.
Using predrilled purlins is a must, as it prevents the material from being "blown out" by nail guns.
Predrilled purlins are a safer and more efficient option, saving you time and resources in the long run.
On the other hand, using drop-in purlins that are "toe-nailed" is a big no-no.
Here are some key differences between predrilled and toe-nailed purlins:
Purlins
Purlins come in two configurations, CEE and ZED, which are shaped on a bending press to create a web with two flanges.
They can run over 30 feet in length, making them a convenient option for larger buildings.
Material for making purlins is almost always cold-formed steel, which is more affordable and easier to work with, but can present structural stability issues.
Local or distortional buckling or lateral displacement can occur, especially under extreme stress or certain conditions.
However, additional stability or support can come from girts, purlins, and eave struts, and additional stiffeners.
The size and number of purlins required will depend on your building's dimensions, primary framing system, and how you plan to use the facility.
CEE purlins have a web height ranging from 4 inches to 20 inches, and flange sizes ranging from 2¼ inches to 5 inches.
The inside bend radius of CEE purlins is typically 0.188 inches, and stiffener lip length is targeted at ⅝ inch.
Steel thickness for CEE purlins ranges from 0.059 inches (16ga) to 0.128 inches (10ga)
On a similar theme: Cee Purlins
Base Angle
Base Angle is a crucial component in purlin design and installation. It's essential to understand its capabilities to ensure a sturdy and secure structure.
The web size of a base angle can range from 2″ to 5″. This variation is important to consider when choosing the right size for your project.
The leg size of a base angle can also vary from 2″ to 5″, providing flexibility in design. This flexibility can be beneficial when working with different materials or designs.
Consider reading: C Purlins Roof Design
The inside bend radius of a base angle is typically 0.188″, which is a critical measurement to keep in mind when designing and installing purlins. This radius can affect the overall stability of the structure.
Steel thickness for base angles can range from 0.059″ (16ga) to 0.128″ (10ga), offering a range of options for different applications.
Welding
Welding should be approached with caution when working with purlins, girts, or bridging. The heat produced in welding can affect the material properties of high yield strength cold-formed steel.
Considerable stress concentrations are likely to arise, even with good quality welding. This can lead to a range of problems down the line.
The protective coating on these materials can be locally removed when welding, which may reduce durability. This is a potential issue that should be taken into account.
Bridging
Bridging plays a crucial role in resisting purlin rotation, which can be a safety hazard during construction.
To prevent misaligned fastenings and excessive purlin rotation, a maximum bridging spacing of 20 times the purlin depth is recommended, but no greater than 4000.
You should use at least one row of bridging in each purlin span to ensure stability.
Exceeding the recommended span/bridging configurations can lead to structural issues, so it's essential to follow the guidelines.
However, if sheeting is installed successfully outside of these recommendations, the published values are still valid for structural purposes.
Girt
Girts play a crucial role in building stability by providing additional support for walls, working in conjunction with columns and wall panels to support vertical load.
They help attach and support wall cladding, which is essential for protecting the building from the elements.
Girts are a type of secondary framing component that improves the strength and stability of walls.
By adding mid-span support, girts enable you to create longer spans, allowing for a wider building.
In fact, girts are often used in conjunction with purlins to create a robust and rigid roof structure.
On a similar theme: How to Support Roof Purlins
Frequently Asked Questions
What is the difference between rafter & purlin?
Rafter and purlin are two types of structural elements in a roof, with rafters providing primary support and purlins serving as a secondary support system to enable heavier roofing materials and expanded design options.
Are purlins load bearing?
Purlins are not load-bearing members themselves, but rather provide secondary support to load-bearing elements in a building's roof and/or walls. They help distribute loads, but rely on primary framing to bear the weight.
When should purlins be used?
Purlins are used in metal roofing and steel frame construction to distribute loads from the roof covering to primary structural elements. They are a crucial component in ensuring the stability and integrity of the roof.
Sources
- https://www.kloecknermetals.com/blog/the-ultimate-guide-to-purlins-in-metal-roofing-steel-frame-construction/
- https://www.westernstatesmetalroofing.com/blog/metal-purlins
- https://info.fbibuildings.com/blog/what-is-a-roof-purlin-and-why-is-it-important
- https://www.chinhdaisteel.com/en/what-makes-good-purlins-2-9-need-to-know-facts-before-purchasing/
- https://www.aepspan.com/purlins/
Featured Images: pexels.com