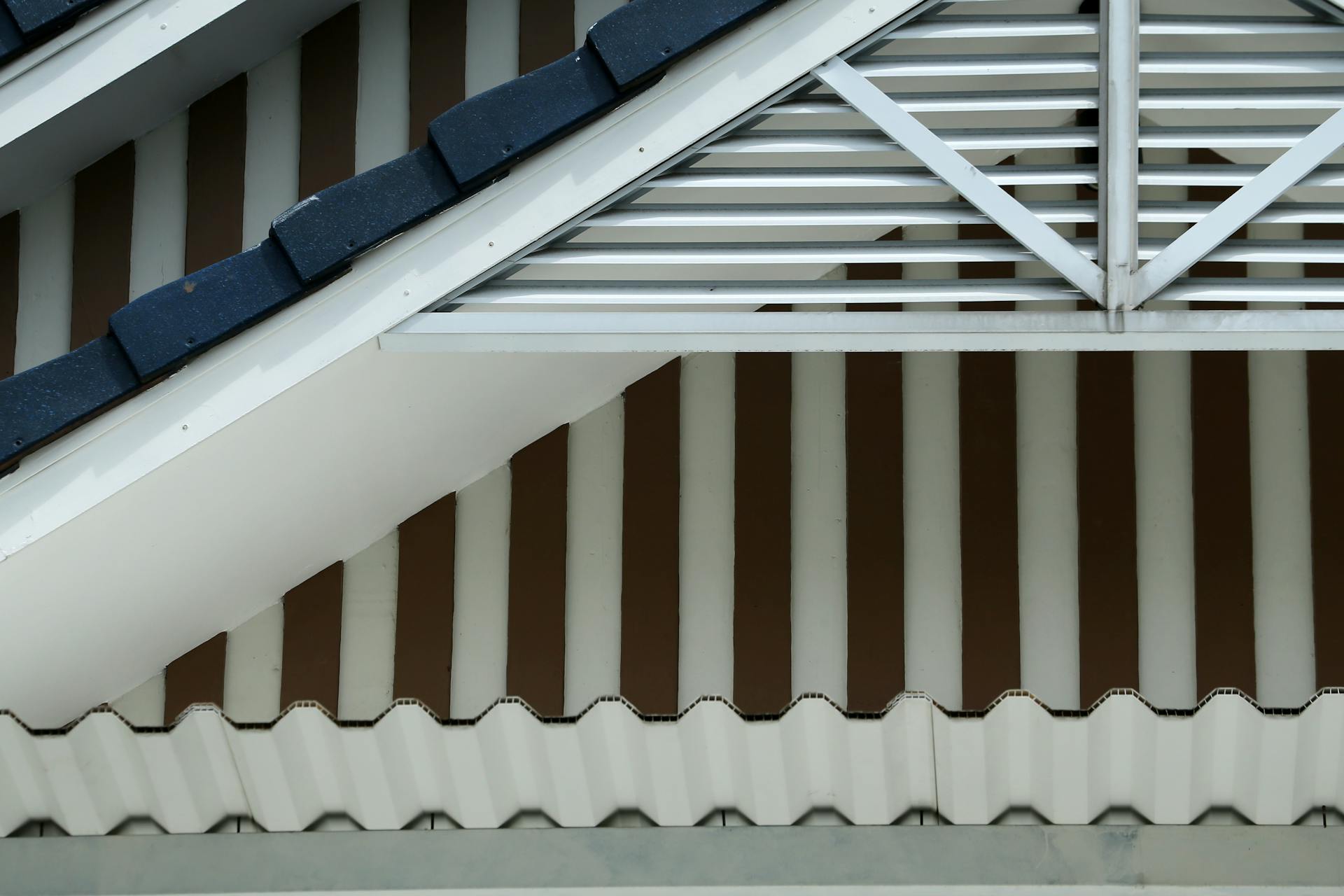
Roof truss connector plates are a crucial component in building construction, providing stability and support to the roof structure. They are designed to connect roof trusses to each other and to the top plate of a wall.
A well-designed connector plate can make all the difference in a roof's durability and safety. According to the article, a connector plate should be designed to transfer loads from the trusses to the wall top plate, ensuring the structure can withstand various weather conditions and loads.
In terms of material selection, aluminum and steel are popular choices for connector plates due to their strength-to-weight ratio. These materials can withstand the stresses and strains of a roof's weight and external forces.
The size and type of connector plate required will depend on the roof's design and load-bearing capacity.
Explore further: Exposed Timber Roof Trusses
Functions and Efficiency
The workhorse of every truss is the metal connector plate that holds the various webs and chords together at the joints.
At a truss joint, the teeth of a connector plate transfer various forces from one wood web or chord into the plate itself.
Shear and axial forces in the truss plate are then transferred across the joint line, where teeth on one side of the joint transfer the forces into the adjoining wood web or chord.
A 3″x6″ plate embedded on both sides of a truss joint would provide 4,264 pounds of lateral resistance.
That's 46 times more than a typical 10d gun nail in SPF #2, which has 94.3 pounds of lateral resistance.
Each of the four plate manufacturers has developed proprietary truss design software that incorporates their plates' performance characteristics based on years and years of testing and evaluation.
Discover more: Parallel Chord Scissor Truss
Inspecting and Repairing
Inspecting potential field damage is crucial during truss installation, especially for long span trusses that are prone to bending out of plane.
Long span trusses can bend excessively, causing damage to truss plates and wood fiber around the joints.
You might like: Long Span Flat Roof
Inspectors should look for rippling on the surface or bending at the edges of truss plates, and also check for plate pull out or embedment gap issues.
The ANSI/TPI 1 Standard requires an embedment gap of 1/32″ or less, which is roughly the thickness of a credit card.
Installers should not use a hammer to try to re-embed truss plates in the field.
Damage to the wood fiber by the connector plate teeth can weaken the strength of a joint.
If plate damage, plate pull out, or wood fiber damage is observed, contact the component manufacturer immediately for advice on a potential repair.
Proper temporary bracing during erection and permanent restraint and bracing over the life of the building can prevent excessive bending and damage.
A different take: Wood Roof Truss Design
Materials and Specifications
The thickness of roof truss connector plates can vary, ranging from 18 gauge to 20 gauge, as seen in the specifications of the "SS" Super-Strength 18 Gauge Plate and the unspecified plate type.
Consider reading: Roof Truss to Top Plate Connection
These plates are made from high-grade steel, with the "SS" Super-Strength 18 Gauge Plate using Grade 60 steel, which is significantly stronger than the Grade 40 steel used in the unspecified plate type.
The number of teeth per square inch also differs between plate types, with the "SS" Super-Strength 18 Gauge Plate having 7 teeth per square inch, whereas the unspecified plate type has 8 teeth per square inch.
Here's a comparison of the thickness and grade of different plate types:
The available widths and lengths of roof truss connector plates also vary, with the "SS" Super-Strength 18 Gauge Plate available in widths from 3.2 inches to 13.1 inches and lengths from 7.0 inches to 24.5 inches, while the unspecified plate type has a narrower range of widths from 1 inch to 12 inches and lengths from 2 inches to 24 inches.
Recommended read: 24 Ft Roof Truss
Specifications
The thickness of some plates is 20 gauge, which is a common thickness for this type of material.
The grade of the "H" High-Strength 20 Gauge Plate is 60, which is stronger than the grade used for the Wave Plate.
The tooth length of the "H" High-Strength 20 Gauge Plate matches the tooth length of the Wave Plate, which is important for roller press compatibility in truss production.
Some plates have a thickness of 20 gauge and a grade of 40.
The "H" High-Strength 20 Gauge Plate was previously known as the "HS" Plate.
Here are the specifications for the "H" High-Strength 20 Gauge Plate:
Some plates have a width of 1” to 12” and a length of 2” to 24”.
SS 18 Gauge
The SS 18 Gauge is a high-performance connector plate that's been designed to work seamlessly with high-strength lumber.
It's made from Grade 60 steel, which is a significant upgrade from other materials used in traditional connector plates.
This plate has a thickness of 18 gauge, making it strong and durable.
Here are some key specifications for the SS 18 Gauge:
The SS 18 Gauge is available in a range of widths, from 3.2 inches to 13.1 inches, and lengths from 7.0 inches to 24.5 inches.
Design and Components
Roof truss connector plates are designed to connect roof trusses to each other and to the top plate of a wall. They are typically made of steel or aluminum.
The most common type of roof truss connector plate is the "splined" connector plate, which is designed to provide maximum strength and stability. It works by allowing the connector plate to slide over the splines on the truss, creating a strong and rigid connection.
Roof truss connector plates are usually installed at the top of each truss, spaced about 24 inches apart.
The Functions
The truss connector plate is a crucial component that holds the various webs and chords together at the joints, transferring forces from one wood web or chord into the plate itself.
It acts like a bridge between one wood member and another, allowing the truss to function as a whole unit.
A truss connector plate, or gang plate, is a type of tie that connects prefabricated light frame wood trusses, produced by punching light gauge galvanized steel to create teeth on one side.
Check this out: Sky Light Roof
These teeth are embedded in and hold the wooden frame components to the plate and each other.
Nail plates, like truss connector plates, are used to connect timber of the same thickness in the same plane, but they are pressed into the side of the timber using tools like a hydraulic press or a roller.
A truss connector plate is manufactured from structural quality steel and is protected with zinc or zinc-aluminum alloy coatings or their stainless steel equivalent.
Here are some common types of truss connector plates:
- Stud ties
- Metal connector plates
- Mending plates
- Nail plates
Note that not all types of nail plates are approved for use in trusses and other structurally critical placements.
Hinge
The Hinge Plate is a crucial component in manufactured housing, made from Grade 40 steel for superior tension and compression values.
It's primarily used on the top chord of the truss, allowing it to be folded down for transportation and raised in place onsite. This makes it a convenient option for construction projects.
The Hinge Plate can also eliminate the need for piggyback trusses, which can be a time-saver for builders.
In side-by-side comparisons, the Hinge Plate meets or exceeds the compression values of competitive products.
Here are some key specs for the Hinge Plate:
*Hinge plate teeth are present in 3 inches of plate length on either end of the plate, with the remainder of the plate containing the hinge.
Addressing Special Conditions
Roof truss connector plates are designed to handle various special conditions, including uneven roof lines and large spans. These conditions require additional support to ensure the structural integrity of the roof.
In cases of uneven roof lines, connector plates can be adjusted to compensate for the difference. This is achieved by using different types of connector plates, such as those with adjustable screws or bolts.
Large spans can be accommodated with specialized connector plates, such as those made from high-strength materials like steel or aluminum. These materials provide the necessary strength and durability to support the weight of the roof.
To ensure proper installation, it's essential to follow the manufacturer's instructions and local building codes. This will help prevent any potential issues or safety hazards.
In areas prone to high winds or seismic activity, connector plates can be designed with additional features, such as reinforced screws or anchor points. These features provide extra security and stability to the roof structure.
By considering these special conditions and using the right connector plates, builders can create strong and durable roofs that withstand various environmental factors.
Frequently Asked Questions
What are the plates on a truss called?
They are commonly referred to as nail plates or metal connector plates.
How do you attach roof trusses to top plates?
To attach roof trusses to top plates, drive a fastener at a 22.5° angle into the center of the truss, engaging the threads in the truss chords. This ensures a secure and precise connection between the truss and top plate.
Are truss plates strong?
Yes, truss plates can provide significant strength, with a 3x6 plate offering 4,264 pounds of lateral resistance. In comparison, a single 10d gun nail has only 94.3 pounds of lateral resistance, highlighting the added security of truss plates.
Sources
- https://framebuildingnews.com/a-powerful-connection/
- https://search.proquest.com/openview/23f14c035037bbc644fa25db0c517d38/1
- https://alpineitw.com/products/connector-plates/
- https://en.wikipedia.org/wiki/Truss_connector_plate
- https://sbcmag.info/sbcextra/2013/fab-five-brief-look-metal-connector-plate-manufacturers
Featured Images: pexels.com