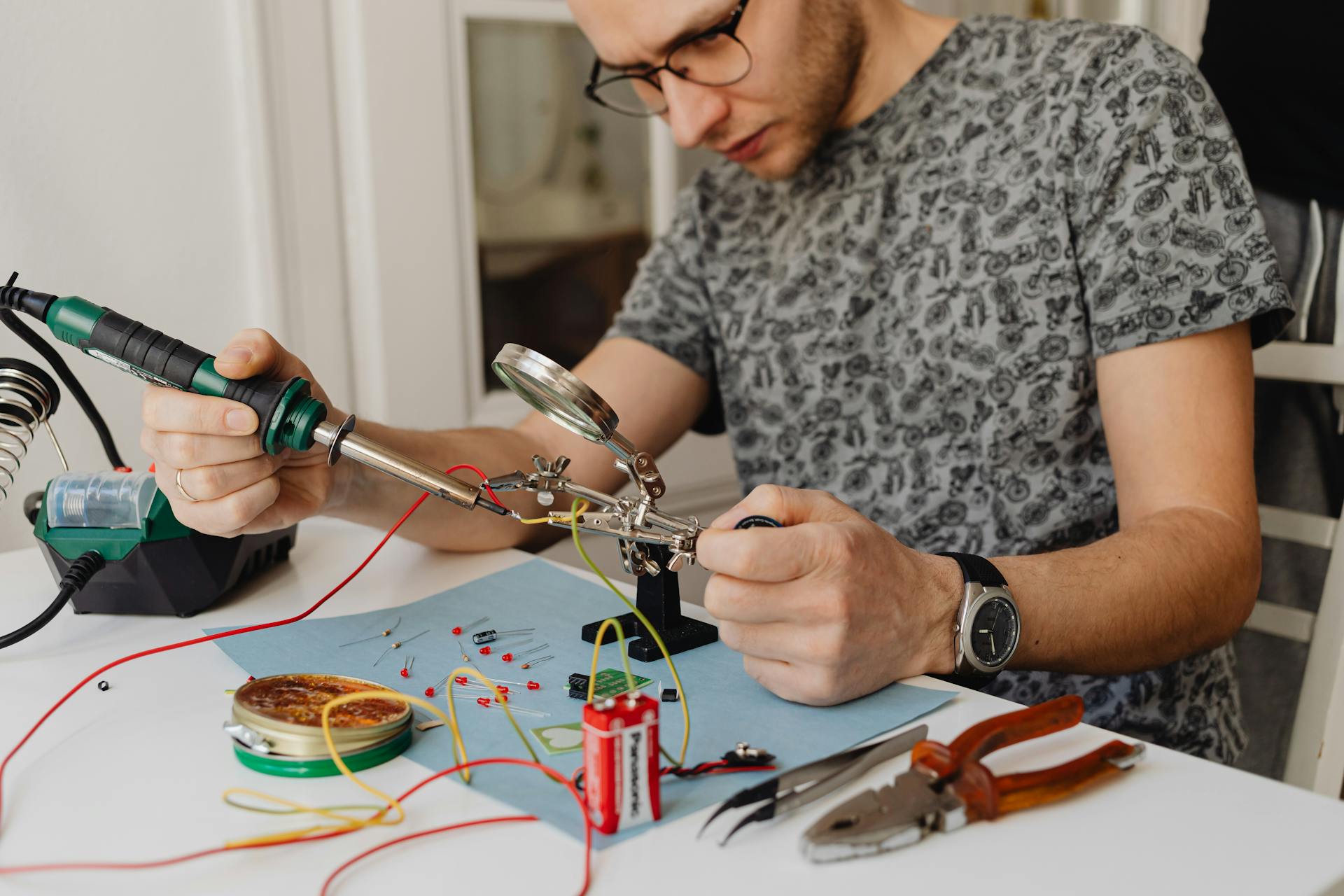
Working with solder for copper water pipes requires a few essential techniques and tools to get the job done right. To start, you'll need a soldering iron with a temperature control, as excessive heat can damage the pipes.
A good soldering iron should have a temperature range of at least 200-400°C to effectively melt the solder. This is crucial for creating a strong bond between the copper pipes.
Proper ventilation is also necessary when soldering, as the flux and solder can release fumes that can be hazardous to your health. A well-ventilated area or a fume extractor can help minimize these risks.
To ensure a clean and smooth soldering process, make sure to clean the pipes and joints thoroughly before applying the solder.
On a similar theme: How Do You Solder Copper Water Pipes
Preparing the Joint
Preparing the Joint involves several crucial steps to ensure a strong, leak-free solder joint. Cleaning and applying flux to the pipe and fitting is essential for proper solder adhesion. This process ensures that the solder flows correctly and adheres to the metal.
Readers also liked: Soldering Water Pipes
You'll need to assemble the pipe and fitting, ensuring they're fully seated. This is a key step in preparing the joint for soldering. Use a propane torch to apply heat to one side of the fitting, moving the flame around the joint to ensure even heating. Watch for the flux to begin bubbling, indicating the joint is hot enough for soldering.
Here's a list of tools and materials you'll need to get ready before starting:
- Tubing cutter
- Reaming tool
- Emery cloth
- Pipe brush
- Flux
- Propane torch
- Solder
- Thick cotton cloth
Preparing the
Preparing the joint requires some careful preparation of the copper pipe and fitting. Cleaning and applying flux is crucial for a strong, leak-free solder joint.
To start, use emery cloth to clean the outside of the pipe end, removing any oxidation or debris. This will ensure a smooth surface for the solder to adhere to.
Cleaning the inside of the fitting is also important. You can use a rolled-up piece of emery cloth or a pipe brush designed for this purpose.
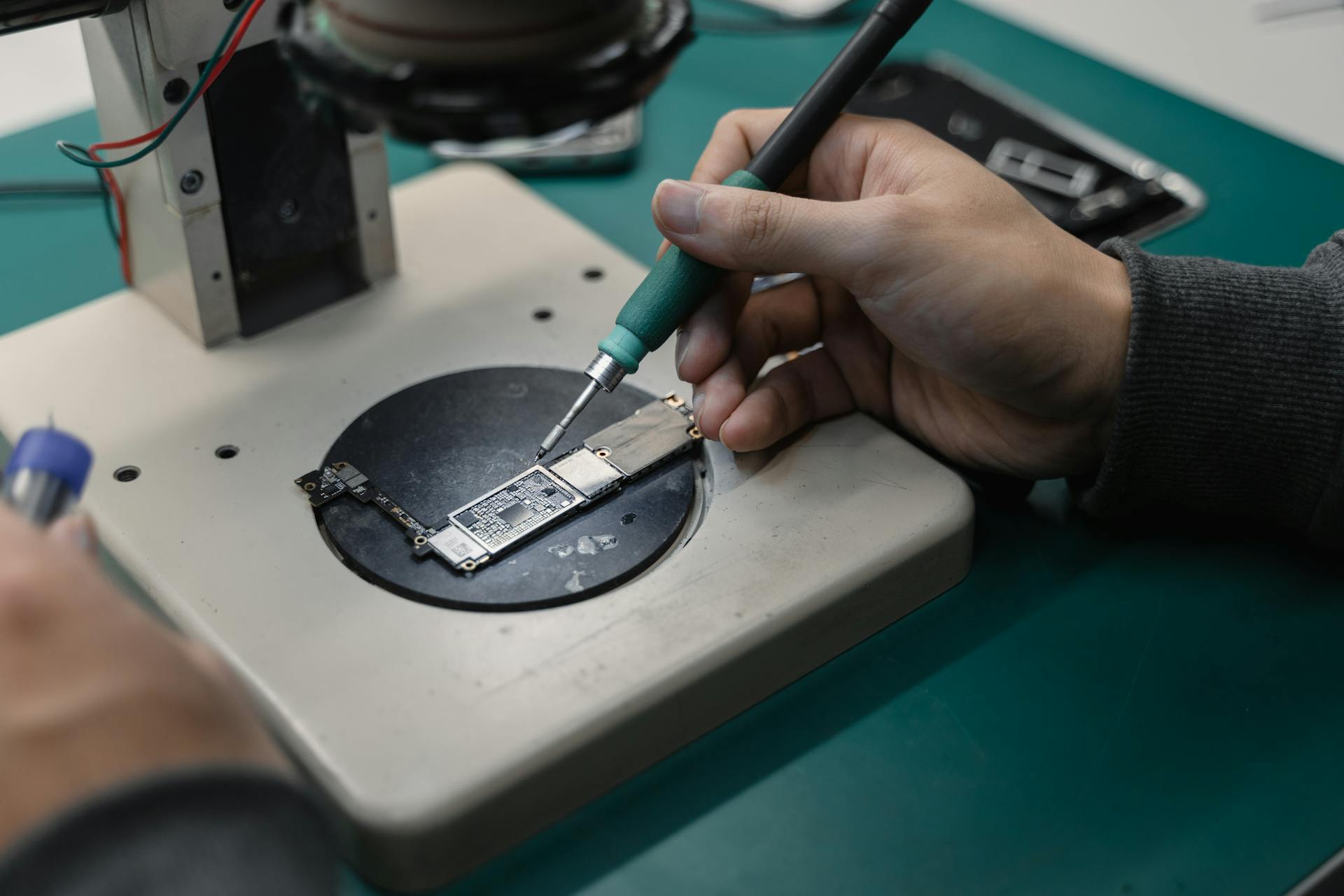
Using a wire-based tool, like a cleaner with small wire bristles, can also be effective for cleaning the outside of the pipe. This will scrape away the oxide layer until the surface is shiny.
Here's a quick rundown of the tools you'll need to clean the pipe and fitting:
- Emery cloth
- Wire-based tool (with small wire bristles)
- Pipe brush (for cleaning the inside of the fitting)
By following these steps, you'll be well on your way to creating a strong, leak-free solder joint.
Joining Different Materials
Joining Different Materials can be a challenge, but it's essential to get it right. Using the wrong connectors or techniques can lead to a weak connection that may leak or fail.
Copper pipe requires specific soldering techniques, so make sure to follow the manufacturer's guidelines. This will ensure a strong and secure connection.
Galvanized steel pipes, on the other hand, need to be joined with the right adapters to prevent corrosion. Using the wrong adapters can lead to a reaction between the materials, causing damage to the pipe.
Check this out: Lead Water Pipes in America
PVC pipes are a bit more forgiving, but it's still crucial to use the correct connectors to avoid any issues. A secure connection is essential to prevent leaks and ensure the pipe's longevity.
Remember, each material has its unique requirements, so take the time to research and understand the specific needs of the pipes you're working with.
Heating the Joint
To assemble the joint properly, ensure the pipe and fitting are fully seated. This is crucial for a strong and leak-free connection.
Use a propane torch to apply heat to one side of the fitting. A "rose bud" shaped flame is ideal for this task, as it will wrap around the joint and heat a wider surface.
Move the flame around the joint to ensure even heating. This is important to prevent scorching, which can lead to failed joints.
Watch for the flux to begin bubbling, indicating the joint is hot enough for soldering. This is a clear sign that the joint is ready for the next step.
If you're using a propane torch, be aware that a cone-shaped flame is not ideal for soldering pipe joints. It's better to use a torch that produces a "rose bud" shaped flame, such as the "TurboTorch" by Thermodyne.
Related reading: How to Heat Water Pipes
The Joint
To solder a copper water pipe joint, you need to assemble the pipe and fitting, ensuring they're fully seated. This is crucial for a strong bond.
Heat application is key to a successful soldering process. Use a propane torch to apply heat to one side of the fitting, then move the flame around the joint to ensure even heating.
The joint is hot enough for soldering when the flux begins to bubble. This is a clear indication that the temperature is right.
Cleaning the pipe and fitting thoroughly before reapplying flux and soldering is essential. This ensures a reliable bond and prevents oxidation from interfering with the soldering process.
Here's a quick rundown of the heating process:
- Assemble the pipe and fitting.
- Use a propane torch to apply heat to one side of the fitting.
- Move the flame around the joint to ensure even heating.
- Watch for the flux to begin bubbling.
Safety Considerations
Wear safety glasses to protect your eyes from solder splatter. Always wear eye protection when soldering, including when working with copper pipes.
Use heat-resistant gloves to prevent burns. Cloth gloves are not advisable, so purchase welders gloves instead.
Work in a well-ventilated area to avoid inhaling fumes. Open windows and doors to allow fresh air to circulate, and consider using a fan to direct fumes away from your workspace.
Keep a fire extinguisher nearby in case of emergencies. A proper fire extinguisher should be rated A, B, and C.
Allow soldered joints to cool completely before handling or testing. This is especially important when working with copper pipes, as a hot joint could break or burn you.
Here are some safety tips to keep in mind:
Maintenance and Troubleshooting
Regular maintenance is key to extending the life of your copper water pipes. Performing regular inspections can help prevent significant damage and costly repairs.
Even the best solder joints can degrade over time due to environmental factors and water quality. This means you need to inspect your soldered joints periodically.
Early detection of signs such as copper corrosion, leaks, or weakening can make all the difference. Regular checks can help you catch these issues before they become major problems.
Common Mistakes to Avoid
Failing to clean the pipe and fitting thoroughly can lead to weak solder joints. This is a crucial step that can make or break the entire process.
Always clean and flux both the pipe and fitting before soldering, as mentioned in "Tips for Successful Soldering".
Applying too much or too little flux can also cause problems. Too little flux won't create a proper seal, while too much can clog the pipe.
The correct amount of flux depends on the specific situation, but it's essential to get it right.
Overheating the joint can damage the pipe or fitting, which is a common mistake to avoid.
Apply heat evenly to avoid creating weak spots in the joint, as advised in "Tips for Successful Soldering".
Moving the pipe before the solder has fully cooled and solidified can also cause issues.
Make sure to allow the joint to cool before testing it, as recommended in "How To Solder Copper Pipes Using 8 Safety Tips".
Forgetting to test the joint for leaks after completion is another mistake to watch out for.
Always test the joint for leaks after completion to ensure a successful soldering experience.
Explore further: Flush Water Pipes in House
Maintenance and Inspections
Regular maintenance and inspections are crucial to ensuring your plumbing system's longevity. Even the best solder joints can degrade over time due to environmental factors and water quality.
To stay on top of things, inspect your soldered joints periodically for signs of copper corrosion, leaks, or weakening. Early detection can prevent significant damage and costly repairs.
It's essential to perform regular maintenance to prevent problems. This includes checking for signs of wear and tear on your plumbing system.
Regular inspections can help you catch issues before they become major problems.
You might like: Types of Water Line Pipes
Selecting Materials and Tools
To get started with soldering copper water pipes, you'll need to gather the right tools and materials. The first step is to get all your tools and materials ready, so you can work efficiently without interruptions.
A tubing cutter is essential for cutting the copper pipes to the right size. A reaming tool is also necessary to smooth out the cut edges. You'll also need some emery cloth to remove any remaining burrs or rough spots.
Here's a list of the basic tools and materials you'll need:
- Tubing cutter
- Reaming tool
- Emery cloth
- Pipe brush
- Flux
- Propane torch
- Solder
- Thick cotton cloth
Cutting Tools and Materials
To cut copper pipe effectively, you'll need the right tools and materials. A tubing cutter is the best tool for cutting copper pipe, as it provides a clean and precise cut.
A close-quarters cutter is a good option for small spaces, but larger cutters are also available and work on the same principle. To use a tubing cutter, place it around the pipe and tighten it until the pipe is clamped between the cutting wheel and the rollers.
Be careful not to over-tighten, as the copper pipe can easily be crushed. To avoid this, tighten the cutter slightly past the point where the cutting wheel first begins to contact the pipe.
You'll also need a reaming tool to remove the small lip on the inside of the pipe produced by the cutter wheel. This lip can cause sediment to accumulate in the pipe, which could eventually plug it.
Here's a list of tools and materials you'll need to get started:
- Tubing cutter
- Reaming tool
- Emery cloth
- Pipe brush
- Flux
- Propane torch
- Solder
- Thick cotton cloth
Remember, having all your tools and materials ready before you start working will save you time and frustration in the long run.
Selecting the Right
Selecting the right materials and tools is crucial for a successful plumbing project.
Lead-free solder is generally recommended for plumbing applications, as it is safe for potable water systems.
Always check to make sure that the solder you select matches the requirements for your specific project.
The right torch can make a big difference in your soldering work. The TurboTorch by Thermodyne is a reliable choice.
A common household propane torch has a cone-shaped flame, which is not ideal for soldering pipe joints.
A "rose bud" shaped flame is what you need to wrap around the joint, heating a wider surface than a pencil point shaped flame could.
The right flux is also essential for a successful joint. Solder will not cohere to copper pipe unless the copper has been chemically treated to receive it.
A water base flux intended for potable use is a must for sweat joints in a potable water system.
Frequently Asked Questions
How long to wait after soldering copper pipe to turn on water?
Wait 30 seconds after soldering copper pipe before turning on water to allow the solder to solidify. If the solder is still molten, water pressure may damage the joint.
What do you put on copper pipe before soldering?
Before soldering, apply a liberal coat of flux to the inside of the fitting and the outside of the copper tubing. This helps ensure a strong, rust-free bond.
Sources
- https://www.thisoldhouse.com/plumbing/21017371/how-to-cut-and-solder-copper-pipe
- https://sawmillcreek.org/showthread.php
- https://www.instructables.com/How-to-Solder-Copper-Pipe-1/
- https://www.balkanplumbing.com/how-to-solder-copper-pipes-safely-correctly/
- http://www.plumbing-geek.com/soldering-copper-pipe.html
Featured Images: pexels.com