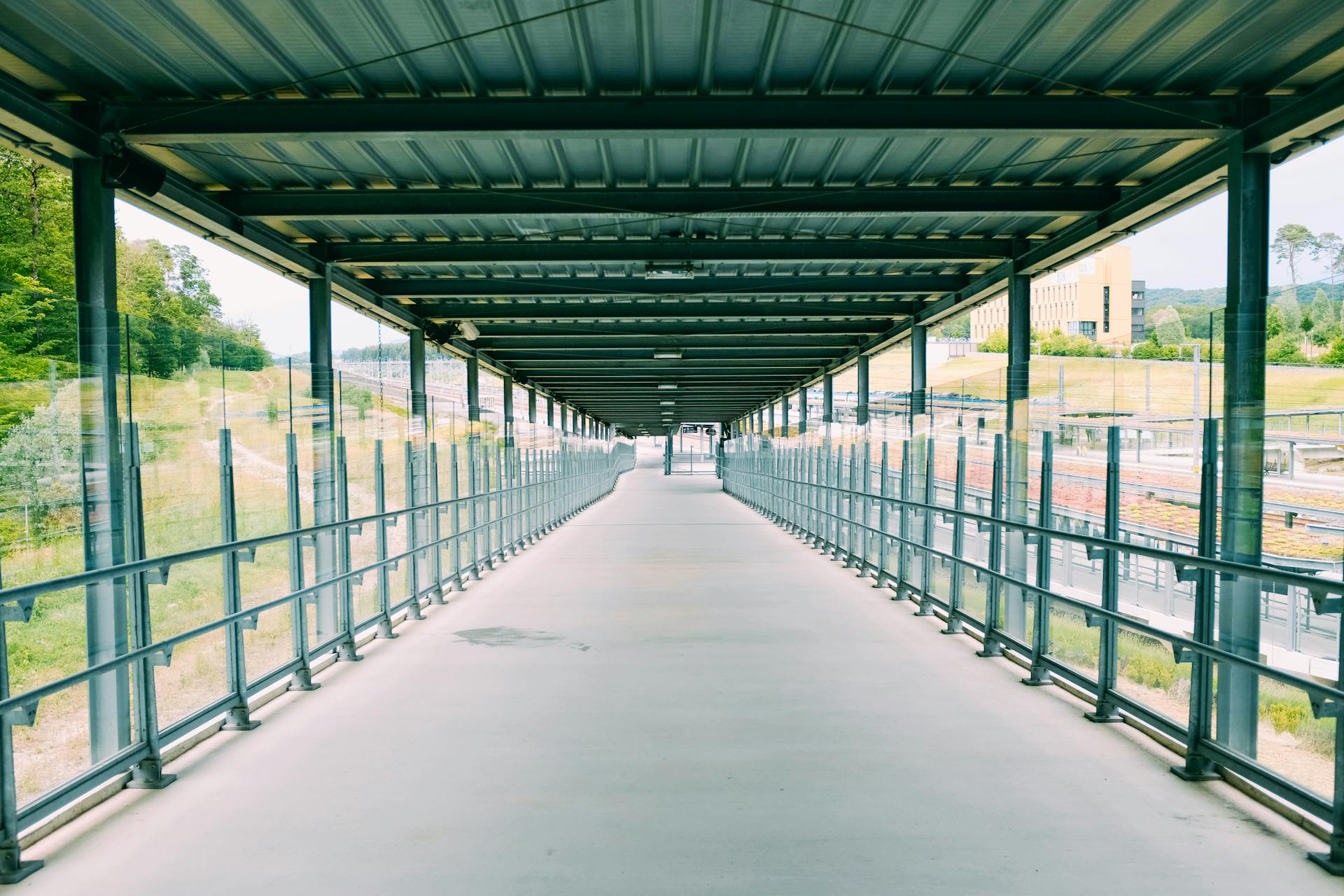
Metal roof purlins or sheathing - it's a crucial part of any metal roofing system. Purlins are horizontal beams that support the metal roof panels, while sheathing is the material that covers the purlins and provides additional support.
Purlins are typically spaced between 2 and 4 feet apart, depending on the design and load requirements of the roof. Sheathing can be made of various materials, including plywood, oriented strand board (OSB), or even metal panels.
A well-designed purlin system can help distribute the weight of the metal roof evenly, reducing the risk of structural damage. Sheathing also helps to prevent water from seeping into the purlin system and causing damage.
Expand your knowledge: How to Support Roof Purlins
What Are Metal Roof Purlins or Sheathing?
Metal roof purlins or sheathing are horizontal beams used in building construction to support and stabilize metal roofing or wall structures.
They are typically made of metal, such as steel, aluminum, or hot-dipped galvanized steel, and come in various shapes, including C purlins and Z purlins.
Metal purlins are placed perpendicular to the roof framing members, like rafters or trusses, and serve as supporting structures, distributing the load of the roof or wall to the main structural elements.
Metal purlins offer several advantages, including their lightweight yet sturdy nature, making them cost-effective and easy to handle during installation.
None
Metal purlins are a crucial component of a metal roof, providing stability and protection. They come in two types: C Purlins and Z Purlins.
The gauge of metal purlins can vary, with options including 12 ga, 14 ga, and 16 ga. This affects their thickness and durability.
Metal purlins are available in a range of sizes, from 4” to 12”. This allows for flexibility in installation and design.
You can choose from two finishes: Red Oxide and Galvanized. Each has its own benefits and is suitable for different applications.
Roofing
Metal roofing systems often feature purlins or sheathing as a crucial component. Purlins are horizontal beams that provide additional support to the roof's structure, typically spaced 2-3 feet apart.
In metal roofing, purlins can be made from a variety of materials, including steel, aluminum, or wood. They help to distribute the weight of the roof evenly, reducing the load on individual rafters.
A well-designed purlin system can increase the overall strength and durability of a metal roof. By providing a solid base for the roofing material, purlins help to prevent water damage and leaks.
Purlins are usually attached to the rafters using screws or nails, creating a secure bond between the two components. This ensures that the purlins remain in place, even in harsh weather conditions.
Sheathing, on the other hand, is a layer of material that covers the purlins and provides a smooth surface for the roofing material to adhere to. It's typically made from plywood or oriented strand board (OSB).
Discover more: Purlins and Rafters
Types of Metal Roof Purlins
Metal purlins are essential components in metal roof construction, providing structural support and stability to the roof or wall structure. They are typically made of metal, such as steel, aluminum, or hot-dipped galvanized steel.
There are two main types of metal purlins: C-purlins and Z-purlins. C-purlins are the most prevalent type and are suitable for various construction scenarios.
Z-purlins, on the other hand, are stronger and often used in heavy-duty applications. They feature a distinctive "Z" shape with ridges on each side, providing additional strength and facilitating secure attachment to rafters or trusses.
Both C-purlins and Z-purlins are available in various sizes and thicknesses, offering flexibility in design and construction.
On a similar theme: How to Install C Purlins
What Are the Types?
Metal purlins come in various shapes, including C purlins and Z purlins, with C purlins being the most prevalent type used in construction scenarios.
C-purlins are widely used due to their versatility, while Z-purlins are stronger and often used in heavy-duty applications.
Metal purlins are typically made of metal, such as steel, aluminum, or hot-dipped galvanized steel, which provides them with a lightweight yet sturdy nature.
C-purlins and Z-purlins are both suitable for supporting metal roofing or wall structures, distributing the load to the main structural elements.
Z-purlins are stronger than C-purlins, but both types offer excellent structural support and durability, making them ideal for various construction projects.
Broaden your view: C Purlins Roof Design
Choosing Between C- and Z-
C-purlins are commonly chosen for applications where effective load transfer and stability are paramount.
Their versatility in accommodating various sizes and thicknesses makes them suitable for multiple projects. C-purlins are the most prevalent metal type, finding application across various construction scenarios.
Z-purlins provide heightened structural strength and secure attachment to rafters or trusses. The ridges on a Z-purlin's distinctive "Z" shape provide additional strength and facilitate secure attachment.
Z-purlins are stronger than C-purlins and are often used in heavy-duty applications. Their adaptability and strength make Z-purlins a preferred choice, ensuring efficient load distribution and structural integrity.
The decision between C-purlins and Z-purlins may depend on factors such as the required load-bearing capacity, the desired level of structural stability, and the architectural preferences of the project.
Galvanized
Galvanized metal purlins are an excellent choice for construction projects requiring maximum durability and corrosion resistance. The galvanization process involves applying zinc-alloy plating to the metal, creating a protective barrier against corrosion.
Galvanized steel purlins are ideal for harsh environments, such as chemical plants or coastal areas, where exposure to saltwater would otherwise lead to rusting in unfinished steel. They outperform non-galvanized alternatives in longevity and resilience.
Galvanized steel purlins are formed of cold-formed steel, which is thin enough for drilling screws through. This type of material is made by rolling multiple sheets together into the desired shape.
Galvanized steel purlins are a better option for all climates because they can contract and expand suitably in extreme temperatures.
Z Section Steel
Z Section Steel purlins are a crucial component in constructing shell structures and pre-engineered metal buildings. They serve as horizontal beams for roof and wall joists, offering superior strength and durability.
Their unique Z shape allows for convenient overlapping during installation, enhancing load-bearing capacity and reducing material usage. This feature is especially beneficial in large-scale structures.
Z purlins are also made from galvanized steel, which provides lasting performance and structural integrity. They're an excellent choice for various building projects due to their strength and durability.
In extreme temperature changes, Z purlins expand and contract reasonably, making them a reliable option. They're also lightweight, dimensionally stable, and have more accuracy compared to wood purlins.
The manufacturing process involves combining lightweight steel structural building products with hot-dipped galvanized steel, providing protection from exposed internal environments. However, contact with incompatible materials should be avoided, and a layer of paint is applied for corrosion protection.
Z purlins are commonly used in industrial and agricultural buildings due to their lightweight and flexible nature. They're also used at overlaps and joints, providing heightened structural strength and secure attachment to rafters or trusses.
Their distinctive "Z" shape with ridges on each side enhances the structural strength of roofing systems, contributing to overall stability and load-bearing capacity. Z purlins resist corrosion and environmental factors, making them a preferred choice for various construction projects.
In contrast to C-purlins, Z purlins are stronger and more reliable, making them suitable for larger-scale structures like commercial or industrial buildings. Their unique appearance and capabilities make them an excellent option for various building projects.
What is Galvanized Steel?
Galvanized steel is a type of steel that's been coated with a layer of zinc to protect it from corrosion.
This process, known as galvanization, involves applying a zinc-alloy plating to the metal, creating a protective barrier that prevents rust and oxidation.
Galvanized steel is ideal for harsh environments, such as coastal areas, where exposure to saltwater would otherwise lead to rusting in unfinished steel.
In fact, galvanized steel outperforms non-galvanized alternatives in longevity and resilience, making it a reliable choice for projects requiring maximum durability.
Galvanized steel purlins are formed of cold-formed steel, which is thin enough for drilling screws through and is made by rolling multiple sheets together into the desired shape.
This type of steel is cost-effective compared to hot-rolled steel and is also easier to work with.
Galvanized steel purlins are lightweight, dimensionally stable, and have more accuracy, making them a better option for all climates.
They can also contract and expand suitably in extreme temperatures, which is why they're a reliable choice for construction projects.
On a similar theme: What Type of Roof Do I Have
Metal Roof Purlin Specifications
Metal roof purlins come in various shapes, including C purlins and Z purlins, and are typically made of metal, such as steel, aluminum, or hot-dipped galvanized steel.
Metal purlins are available in different sizes, including 12g (up to 21 inches), 14g (up to 24 inches), and 16g (up to 16 inches), allowing for flexibility in accommodating different structural requirements.
Standard metal purlin sizes are manufactured in lengths of 100mm, 150mm, 200mm, 250mm, and 300mm, equivalent to 4 inches, 6 inches, 8 inches, 10 inches, and 12 inches.
Metal purlins come in various gauges, including 12 gauge, 14 gauge, and 16 gauge, each with its unique strength and load-bearing capabilities, making it essential to select the most suitable gauge for optimal structural support.
Consulting an engineer or a technical personnel can help determine the best gauge to fit your building, ensuring the necessary strength and reliability for a robust and long-lasting structure.
Curious to learn more? Check out: Zed Purlins Sizes
Details on RHS
RHS purlins are a unique type of purlin that is used in roofs where the support structure is visible after the project is complete.
They are available in hollow and rectangular tubes instead of steel bars. This design makes them a great option for projects where aesthetics are a top priority.
Metal purlins, including RHS purlins, are typically made of metal, such as steel, aluminum, or hot-dipped galvanized steel. This material choice provides excellent structural support and durability.
RHS purlins can be used in a variety of building types, including commercial and industrial buildings, as well as some residential metal roofs.
Curious to learn more? Check out: How Do Green Roofs Compare to Traditional Roofs
Sizes
Metal purlin sizes range from 12g (up to 21 inches) to 16g (up to 16 inches), offering flexibility in accommodating different structural requirements.
You can choose from a variety of finishes, including red oxide, gray, and galvanized, to select the most suitable purlins for your projects.
Purlins are also available in standard sizes of 100mm (4 inches), 150mm (6 inches), 200mm (8 inches), 250mm (10 inches), and 300mm (12 inches).
Spacing
Spacing is crucial for metal roof purlins, and it's determined by the weight the structure will carry and the load capacity of the metal panels.
The heavier the expected load, the shorter the distance between purlins. At ETAS, they collaborate with clients to assess project requirements and calculate the correct purlin spacing.
The ideal spacing of purlins is typically two feet apart, as seen in the installation process. This spacing is a good starting point, but it may need to be adjusted based on the specific project requirements.
A shorter spacing between purlins means more purlins are needed, which can increase the cost of materials. However, finding the optimal purlin spacing can help clients achieve cost-efficiency without compromising the structural integrity of their project.
The load charts provided by ETAS help determine the optimal spacing for each job, taking into account the metal panel and purlin load capacity. This ensures a safe and reliable construction.
Here's an interesting read: Roofing Purlins Spacing
Gauges
Metal purlins come in a range of gauges, including 12 gauge, 14 gauge, and 16 gauge. Each gauge has its unique strength and load-bearing capabilities.
The choice of gauge depends on the specific requirements and demands of the construction project. This is because each gauge has its own strengths and weaknesses.
To determine the exact gauge for your building, consult an engineer. Our technical personnel can also determine the best gauge to fit your building.
At ETAS, our team of experts collaborates closely with our clients to assess the project’s needs and recommend the best purlin gauge accordingly.
Frequently Asked Questions
Do you put sheathing under a metal roof?
Sheathing is typically installed under a metal roof to provide a solid base and prevent moisture damage. Proper installation of sheathing is essential for a metal roof's expected lifespan of 40-70 years.
Can you walk on a metal roof with purlins?
Yes, a metal roof with purlins is walkable when dry, but be cautious in wet conditions.
Sources
- https://www.kloecknermetals.com/blog/the-ultimate-guide-to-purlins-in-metal-roofing-steel-frame-construction/
- https://etas-inc.com/metal-roofing-purlins/
- https://www.steelandstud.com/purlins-for-metal-roof/
- https://ezibatten.com/blog/details-you-ought-to-know-about-roof-purlins-and-battens/
- https://ezibatten.com/blog/explore-how-roof-battens-and-purlins-can-be-the-right-choice-for-your-project/
Featured Images: pexels.com